FENECON Home 6, 10 & 15 assembly and operating instructions
1. About these instructions
Personnel must have carefully read and understood these installation and service instructions before starting any work.
1.1. Manufacturer
FENECON GmbH
Gewerbepark 6
94547 Iggensbach
Germany
Phone: +49 (0) 9903 6280 0
Fax: +49 (0) 9903 6280 909
E-mail: service@fenecon.de
Internet: www.fenecon.de
1.2. Information on these operating instructions
© FENECON GmbH, 2025
All rights reserved.
Reprinting, even in part, is only permitted with the permission of FENECON GmbH.
1.3. Version/revision
Version/ Revision |
Änderung |
Datum |
Name |
2024.06.1 |
Entwurf Erstellung |
10.06.2024 |
FENECON GW |
2024.11.1 |
Fertigstellung |
14.11.2024 |
FENECON MR |
2024.11.2 |
Update - Illustrationen |
20.11.2024 |
FENECON MR |
2024.11.3 |
Update - Lieferumfang |
29.11.2024 |
FENECON MR |
2025.1.1 |
Integration Feuerwehrhinweis |
27.01.2025 |
FENECON PM |
2025.8.1 |
Integration Splitsockel |
01.08.2025 |
FENECON TK/MR |
1.4. Symbol conventions
|
||
|
||
|
||
|
1.5. Structure of warning notices
If observed, warnings protect against possible personal injury and damage to property. The signal word to classifies the magnitude of danger.
Source of the danger
|
Danger sign
The danger sign indicates warnings that warn of personal injury.
Source of danger
The source of danger indicates the cause of the hazard.
Possible consequences of non-compliance
The possible consequences of ignoring the warning are, for example, crushing, burns or other serious injuries.
Measures/Prohibitions
Measures/prohibitions include actions that must be taken to avoid a hazard (e.g. stopping the drive) or that are prohibited to avoid a hazard.
1.6. Terms and abbreviations
The following terms and abbreviations are used in the installation and service instructions:
Term/abbreviation | Meaning |
---|---|
AC |
Alternating Current |
CHP |
Combined Heat and Power plant/unit |
BMS |
Battery Management System |
DC |
Direct Current |
EMS |
Energy Management System |
Energy meter |
Electricity meter for the inverter at the grid connection point |
FEMS |
FENECON Energy Management System |
Commissioning |
Commissioning |
MPPT |
Maximum Power Point Tracking Finder for the maximum power point |
GCP |
Grid Connection Point |
PE |
Protective conductor |
PV |
Photovoltaic |
RTE |
Round-Trip-Efficiency (RTE) |
SG-Ready |
Smart-Grid-Ready — Preparation of the heat pump for external control |
SoC |
State of Charge |
SoH |
State of Health — State of ageing |
VDE |
German Association for Electrical, Electronic & Information Technologies e. V. |
Widget |
Component of Online Monitoring |
1.7. Scope of delivery
Item | Component | Amount | Comment |
---|---|---|---|
1 |
FENECON Home 6, 10 & 15 inverter |
1 |
Model is system-dependent (6, 10 or 15 kW) |
2 |
FENECON Home 6, 10 & 15 EMS box |
1 |
FENECON Energy Management System incl. |
3 |
FENECON Home 6, 10 & 15 Parallel switch box |
1 |
optional for second FENECON Home 6, 10 & 15 battery tower |
4 |
FENECON Home 6, 10 & 15 Extension box |
1 |
optional for third and fourth FENECON Home 6, 10 & 15 battery tower |
5 |
FENECON Home 6, 10 & 15 BMS box |
1 |
per FENECON Home 6, 10 & 15 battery tower |
6 |
FENECON Home 6, 10 & 15 Battery module |
depending on the capacity ordered |
|
7 |
FENECON Home 6, 10 & 15 Base |
1 |
per FENECON Home 6, 10 & 15 battery tower |
Component | Comment |
---|---|
Installation and service instructions |
Manual for the installer |
Quick start guide FENECON Home 6, 10 & 15 |
Quick start guide for the installer |
1.8. Applicable documents
All documents listed in the appendix to these installation and service instructions must be observed. See 15.1 Applicable documents.
1.9. Availability
The operator must keep these installation and service instructions or relevant parts of them within easy reach in the immediate vicinity of the product.
If the product is handed over to another person, the operator passes these installation and service instructions on to that person.
2. Sicherheit
2.1. Bestimmungsgemäße Verwendung
Das FENECON-Stromspeichersystem dient dem Speichern von elektrischer Energie in wiederaufladbaren Lithium-Eisenphosphat-Batteriemodulen (Beladen) und dem Bereitstellen von elektrischer Energie (Entladen). Dieser Be- und Entladeprozess erfolgt über einen angeschlossenen Wechselrichter. Die Anlage darf nur unter Einhaltung der zulässigen technischen Daten (siehe Kapitel [Technische Daten]) verwendet werden.
FENECON-Stromspeichersysteme bestehen aus verschiedenen Modulen. Dazu gehören insbesondere ein BMS (Batteriemanagementsystem), das FENECON Energy Management System (FEMS), Batteriemodule und Sockel. Alle Prozesse des Stromspeichersystems werden durch das FEMS überwacht und gesteuert.
Jede andere Verwendung ist keine bestimmungsgemäße Verwendung.
2.2. Vernünftigerweise vorhersehbare Fehlanwendung
Alle Anwendungen, die nicht zu den Vorgaben der bestimmungsgemäßen Verwendung zählen gelten als Fehlanwendung.
Arbeiten an unter Spannung stehenden Teilen sind generell nicht zulässig. Elektroarbeiten dürfen nur von Elektrofachkräften durchgeführt werden.
Bei allen Arbeiten an elektrischen Komponenten sind die folgenden Sicherheitsregeln einzuhalten:
-
Disconnect.
-
Secure against restarting.
-
Check that there is no voltage.
-
Earth and short-circuit.
-
Cover or shield neighboring live parts.
Die Nichteinhaltung der Sicherheitsregeln wird als vernünftigerweise vorhersehbare Fehlanwendung betrachtet. |
Weitere Fehlanwendungen sind insbesondere:
-
unsachgemäßer Transport, Aufstellung bzw. Aufbau an einem Ort, Probebetrieb oder Betrieb durch den das System Schaden nehmen kann.
-
Veränderung der angegebenen Leistungsdaten, auch der einzelnen Komponenten.
-
Veränderung bzw. Abweichung der angegebenen Anschlusswerte.
-
funktionelle oder bauliche Veränderungen.
-
Betreiben des Produkts im fehlerhaftem bzw. defekten Zustand.
-
unsachgemäße Reparaturen.
-
der Betrieb ohne Schutzeinrichtungen oder mit defekten Schutzeinrichtungen.
-
Missachtung der Angaben der Original-Betriebsanleitung.
-
unerlaubter bzw. unautorisierter Zugriff über die Steuerung oder das Netzwerk.
-
das Einspielen von Firmware-Updates, die nicht über FENECON bezogen wurden.
-
Feuer, offenes Licht und Rauchen in der Nähe des Speichersystems.
-
unzureichende Belüftung am Aufstellort.
-
eigenmächtige Änderungen und Handlungen am Speichersystem.
-
Einsatz als mobiler Energiespeicher.
-
direkter Einsatz in einem PV-System (Eine Einbindung über ein AC-gekoppeltes Netz ist möglich).
2.3. Einsatzbereich — Elektromagnetische Verträglichkeit (EMV)
Das Niederspannungsbetriebsmittel ist für die Verwendung in folgenden Einsatzbereichen bestimmt:
-
Allgemeinheit (öffentlich)
Die Verwendung in anderen Einsatzbereichen ist nicht bestimmungsgemäß.
2.4. Qualifikation des Personals
Zur bestimmungsgemäßen Verwendung, Installation und Wartung der Anlage muss qualifiziertes Personal eingesetzt werden. Verantwortungsbereich, Zuständigkeit und Überwachung des Personals müssen durch den Betreiber genau geregelt sein.
2.4.1. Elektrofachpersonal
Zu Elektrofachpersonal zählen Personen, die:
-
aufgrund Ihrer fachlichen Ausbildung, Kenntnisse und Erfahrungen sowie Kenntnis der einschlägigen Normen und Bestimmungen in der Lage sind, Arbeiten an elektrischen Anlagen auszuführen.
-
vom Betreiber zum Ausführen von Arbeiten an elektrischen Anlagen und Ausrüstungen des Batteriesystems beauftragt und geschult worden sind.
-
mit der Funktionsweise des Batteriesystems vertraut sind.
-
auftretende Gefährdungen erkennen und diese durch geeignete Schutzmaßnahmen verhindern können.
2.5. Allgemein zum FENECON-Speichersystem
Das Produkt ist so zu platzieren, dass ausreichend Bewegungsraum für das Service- und Instandhaltungspersonal in jeder Lebensphase des Produkts gewährleistet werden kann. Die Lebensdauer des Produkts hängt von den Standzeiten und Wartungsintervallen ab, die vom Fachpersonal durchgeführt werden. Die Standzeit wird besonders durch eine vorbeugende Instandhaltung und Wartung beeinflusst.
-
Die Installation der Batteriemodule und die Herstellung der Kabelverbindungen dürfen nur durch Elektrofachpersonal erfolgen.
-
Das Stromspeichersystem darf nur unter den bestimmten Lade-/Entladebedingungen benutzt werden (vgl. Kapitel [Technische Daten]).
-
Das Stromspeichersystem von Kindern und Tieren fernhalten.
-
Die Steckkontakte der BMS-Box nicht umgekehrt anschließen.
-
Batteriemodule nicht kurzschließen.
-
Die Batteriemodule nur bestimmungsgemäß verwenden.
-
Die nicht bestimmungsgemäße Verwendung kann zu Überhitzung, Explosion oder Brand der Batteriemodule führen.
-
-
Die Anweisungen zur Installation und zum Betrieb lesen, um Schäden durch fehlerhafte Bedienung zu vermeiden.
-
Die Batteriemodule können möglicherweise nach längerer Lagerzeit über eine zu geringe Zellspannung verfügen. Sollte dies der Fall sein, wenden Sie sich an den Service
-
Die Batteriemodule keinen Hochspannungen aussetzen.
-
Die Batteriemodule auf ebenen Flächen abstellen.
-
Keine Gegenstände auf den FENECON-Batterietürmen abstellen.
2.5.1. Elementareinflüsse
-
Das Stromspeichersystem von Wasserquellen fernhalten.
-
Das Stromspeichersystem nicht in Wasser eintauchen, befeuchten oder mit nassen Händen berühren.
-
Das Stromspeichersystem an kühlen Orten aufstellen/lagern.
-
Stromspeichersystem nicht erhitzen.
-
Das Stromspeichersystem keinem offenen Feuer aussetzen.
-
Das Stromspeichersystem nicht in der Nähe von offenem Feuer, Heizungen oder Hochtemperaturquellen aufstellen oder benutzen.
-
Aufgrund der Hitze können Isolationen schmelzen und die Sicherheitsentlüftung beschädigt werden. Dies kann zu Überhitzung, Explosion oder Bränden an den Batteriemodulen führen.
-
-
Es dürfen keine Lötarbeiten am Stromspeichersystem durchgeführt werden. Während des Lötens eingebrachte Wärme kann den Isolator und den Mechanismus der Sicherheitsentlüftung beschädigen und zu Überhitzung, Explosion oder Brand der Batteriemodule führen.
2.5.2. Mechanische Einflüsse
-
Die Batteriemodule dürfen nicht zerlegt oder verändert werden. Die Batteriemodule enthalten einen Sicherheitsmechanismus und eine Schutzeinrichtung, deren Beschädigung zu Überhitzung, Explosion oder Brand der Batteriemodule führen kann.
-
Nicht auf das Stromspeichersystem treten.
-
Nicht versuchen, Batteriemodule zu quetschen oder zu öffnen.
-
Keine mechanische Gewalt auf das Stromspeichersystem einwirken lassen.
-
Die Batteriemodule können beschädigt werden und es kann zu Kurzschlüssen kommen, was zu Überhitzung, Explosion oder Brand der Batteriemodule führen kann.
-
-
Teile des Stromspeichersystems nicht werfen oder fallen lassen.
-
Defekte oder heruntergefallene Batteriemodule nicht mehr verwenden.
-
-
Das Stromspeichersystem nicht mehr verwenden, wenn während der Montage, des Ladens, des normalen Betriebs und/oder der Lagerung Farbveränderungen oder mechanische Schäden festgestellt werden.
-
Wenn die Schutzvorrichtungen beschädigt sind, können abnormale Ladeströme und -spannungen eine chemische Reaktion in den Batteriemodulen verursachen, die zu Überhitzung, Explosion bis hin zum Brand der Batteriemodule führen.
2.5.3. Installation, Betrieb und Wartung
Bei Instandhaltungs-, Wartungs- und Reinigungsarbeiten sicherstellen, dass das Produkt sicherheitsgerichtet abgeschaltet und gegen Wiedereinschalten gesichert ist. Zudem müssen alle Anweisungen in dieser Betriebsanleitung befolgt werden. |
Bei Installation, Betrieb oder Wartung der Batteriemodule unbedingt die folgenden Sicherheitshinweise beachten:
-
Installations-/Wartungsarbeiten und die Herstellung der Kabelverbindungen dürfen nur von Fachpersonal (Elektrofachpersonal) durchgeführt werden.
-
Bei den Wartungsarbeiten auf trockene Isoliergegenstände stellen und während der Wartungsarbeiten/des Betriebs keine Metallgegenstände (z. B. Uhren, Ringe und Halsketten) tragen.
-
Isolierte Werkzeuge benutzen und persönliche Schutzausrüstung tragen.
-
Nicht zwei geladene Kontakte mit Potentialdifferenz berühren.
-
Die Batteriespannung mit einem Multimeter messen und sicherstellen, dass die Ausgangsspannung im Aus-Modus 0 V beträgt.
-
Wenn eine Anomalie festgestellt wird, den Batterieturm sofort ausschalten.
-
Die Wartungsarbeiten erst fortsetzen, nachdem die Ursachen der Anomalie beseitigt wurden.
-
Die Batteriemodule können einen Stromschlag und durch hohe Kurzschlussströme Verbrennungen verursachen.
-
Die Batteriemodulstecker (+) und (-) nicht direkt mit einem Draht oder einem metallischen Gegenstand (z. B. Metallkette, Haarnadel) berühren. Bei Kurzschluss kann übermäßig Strom erzeugt werden, der zu Überhitzung, Explosion oder Brand der Batteriemodule führen kann.
2.5.4. Brandschutz
-
Das Stromspeichersystem nicht direktem Sonnenlicht aussetzen.
-
Den Kontakt mit leitfähigen Gegenständen (z. B. Drähten) vermeiden.
-
Hitze- und Feuerquellen, brennbare, explosive und chemische Materialien vom Stromspeichersystem fernhalten.
-
Explosionsgefahr: Batteriemodule nicht im Feuer entsorgen!
2.5.5. Lagerung
-
Bereich: Brandsicher im Innen-/Außenbereich mit geeignetem Witterungsschutz.
-
Lufttemperatur: -20 °C bis 40 °C.
-
Relative Luftfeuchtigkeit: max. 50 % bei +40 °C.
-
Batteriemodule (Lithium-Eisenphosphat-Batterien) nicht mit brennbaren oder giftigen Gegenständen lagern.
-
Batteriemodule mit Sicherheitsmängeln separat von unbeschädigten Batteriemodulen lagern.
Lagerung länger als 12 Monate
|
2.6. Betriebsmittel
2.6.1. Electrolyte solution of the battery modules
-
Electrolyte solution is used in the battery modules (lithium iron phosphate).
-
The electrolyte solution in the battery modules is a clear liquid and has a characteristic odor of organic solvents.
-
The electrolyte solution is flammable.
-
The electrolyte solution in the battery modules is corrosive.
-
Do not inhale the vapors.
-
If the electrolyte solution is swallowed, induce vomiting.
-
Leave the contaminated area immediately after inhaling the vapors.
-
Eye and skin contact with leaked electrolyte solution must be avoided.
-
Contact with electrolyte solution can cause severe burns to the skin and damage to the eyes.
-
After skin contact: Immediately wash skin thoroughly with neutralizing soap and consult a doctor if skin irritation persists.
-
After eye contact: Immediately flush eye(s) with running water for 15 minutes and seek medical advice.
-
Delayed treatment can cause serious damage to health. |
2.7. Restrisiko
Warnung vor elektrischer Spannung Arbeiten an elektrischen Ausrüstungen nur durch Elektrofachkräfte vom Hersteller oder durch speziell beauftragte, unterwiesene Elektrofachkräfte und unter Beachtung der Sicherheitsvorschriften durchführen lassen. |
Unbekannte Störmeldungen Unbekannte Störung und der Versuch der Behebung können zu Schäden am Produkt führen. |
Alle Türen, Notausgänge und Bereiche um das Speichersystem herum müssen frei bleiben, Fluchtwege nicht verstellen! |
Die Bodenbeschaffenheit außerhalb des Speichersystems ist in der Verantwortlichkeit des Nutzers. Jedoch ist das Gehäuse dicht gebaut, so dass kein Elektrolyt austreten kann. |
2.8. Verhalten in Notsituationen
In Notsituationen wie folgt vorgehen:
-
Das Stromspeichersystem vom Netz trennen.
-
Aus dem Gefahrenbereich entfernen.
-
Den Gefahrenbereich absichern.
-
Die Verantwortlichen informieren.
-
Gegebenenfalls Arzt alarmieren.
2.9. Pictograms
Pictograms on the system indicate dangers, prohibitions and instructions. Illegible or missing pictograms must be replaced by new ones.
Pictogram | Meaning | Description |
---|---|---|
Pictogram on enclosure warning of dangerous voltage |
Pictogram on enclosure and marking of components which do not clearly indicate that they contain electrical equipment which may be a risk of electric shock. |
|
General warning sign. |
||
Battery charging hazard warning |
Pictogram on the enclosure and marking of components which do not clearly indicate that they contain electrical equipment which may be the cause of a risk due to battery charging. |
|
No open flames; fire, open sources of ignition and smoking prohibited |
Pictogram on the enclosure and marking of components which do not clearly indicate that they contain electrical equipment which may give rise to a risk from open flames, fire, open sources of ignition and smoking. |
|
Protective earth marking. |
||
Separate collection of electrical and electronic equipment. |
||
Observe instructions. |
||
Use protective headgear |
||
Use protective footwear |
||
Use protective gloves |
||
CE label |
||
Product is recyclable. |
2.10. Operating materials/equipment
2.10.1. Electrolyte solution of the battery modules
-
Electrolyte solution is used in the battery modules (lithium iron phosphate).
-
The electrolyte solution in the battery modules is a clear liquid and has a characteristic odor of organic solvents.
-
The electrolyte solution is flammable.
-
The electrolyte solution in the battery modules is corrosive.
-
Contact with electrolyte solution can cause severe burns to the skin and damage to the eyes.
-
Do not inhale the vapors.
-
If the electrolyte solution is swallowed, induce vomiting.
-
Leave the contaminated area immediately after inhaling the vapors.
-
Eye and skin contact with leaked electrolyte solution must be avoided.
-
After skin contact: Immediately wash skin thoroughly with neutralizing soap and consult a doctor if skin irritation persists.
-
After eye contact: Immediately flush eye(s) with running water for 15 minutes and seek medical advice.
-
Delayed treatment can cause serious damage to health.
2.10.2. Electrical equipment
-
Work on electrical equipment may only be carried out by qualified electricians.
-
The five safety rules must be observed for all work on electrical components:
-
Disconnect.
-
Secure against restarting.
-
Check that there is no voltage.
-
Earth and short-circuit.
-
Cover or shield neighboring live parts.
-
-
Maintenance work may only be carried out by trained specialist personnel (service personnel).
-
Before starting work, carry out visual checks for insulation and housing damage.
-
The system must never be operated with faulty or non-operational electrical connections.
-
To avoid damage, lay supply lines without crushing and shearing points.
-
Only insulated tools must be used for maintenance on uninsulated conductors and terminals.
-
Switch cabinets (e. g. inverter housing) must always be kept locked. Only authorized personnel with appropriate training and safety instructions (e. g. service personnel) should be allowed access.
-
The inspection and maintenance intervals for electrical components specified by the manufacturer must be observed.
-
To avoid damage, lay supply lines without crushing and shearing points
-
If the power supply is disconnected, specially marked external circuits may still be live!
-
Some equipment (e. g. inverters) with an electrical intermediate circuit can still carry dangerous residual voltages for a certain time after disconnection. Before starting work on these systems, check that they are voltage-free.
2.11. Personal protective equipment
Depending on the work on the system, personal protective equipment must be worn:
-
Protective footwear
-
Protective gloves, cut-resistant if necessary
-
Protective eyewear
-
Protective headgear
2.12. Spare and wear parts
The use of spare and wear parts from third-party manufacturers can lead to risks. Only original parts or spare and wear parts approved by the manufacturer may be used. The instructions for spare parts must be observed. Further information can be found in the wiring diagram.
Further information must be requested from the manufacturer. |
2.13. IT security
FENECON energy storage systems and their applications communicate and operate without internet connection. The individual system components (inverters, batteries, etc.) are not directly connected to the internet or accessible from the internet. Sensitive communications via the internet are processed exclusively via certificate-based TLS encryption.
Access to the programming levels is not barrier-free and is accessible at different levels depending on the qualifications of the operating personnel. Safety-relevant program changes require additional verification.
FENECON processes energy data of European customers exclusively on servers in Germany and these are subject to the data protection regulations applicable in this country.
The software used is checked using automated tools and processes established during development in order to keep it up to date and to rectify security-relevant vulnerabilities at short notice. Updates for FEMS are provided free of charge for life.
3. Technical data
3.1. General technical data
Description | Value/dimension | |
---|---|---|
Installation/environmental conditions |
Protection specification |
IP55 |
Operating altitude above sea level |
≤ 2,000 m |
|
Installation/operating temperature |
-35 °C to +60 °C |
|
Relative humidity (operation/storage) |
50 % non-condensing (up to 90 % permissible for short periods) |
|
Battery operating temperature |
-20 °C to +55 °C |
|
Optimal operating temperature of the battery |
+15 °C to +30 °C |
|
Cooling |
Natural convection |
|
Noise level |
< 30 dB |
|
Max. grid connection |
120 A |
|
Certification/Directive |
Complete system |
CE |
Inverter |
VDE 4105:2018-11 |
|
Battery |
UN38.3 |
3.2. Technical data — Inverter
Benennung |
Wert/Größe |
|||
Wechselrichter-Modell |
FINV-6-2-DAH |
FINV-10-2-DAH |
FINV-15-2-DAH |
|
DC-PV-Anschluss |
Max. DC-Eingangsleistung |
9 kWp |
15 kWp |
22,5 kWp |
MPP-Tracker |
2 |
3 |
3 |
|
Eingänge je MPPT |
1 (MC4) |
1 (MC4) |
1(MC4) |
|
Startspannung |
120 V |
120 V |
120 V |
|
Max. DC-Eingangsspannung in V |
1000 V |
1000 V |
1000 V |
|
MPPT-Spannungsbereich |
120 V bis 850 V |
120 V bis 850 V |
120 V bis 850 V |
|
Nenn-Eingangsspannung in V |
620 V |
620 V |
620 V |
|
Max. Eingangsstrom je MPPT |
16 A |
16 A |
16 A |
|
Max. Kurzschlussstrom je MPPT |
24 A |
24 A |
24 A |
|
AC-Anschluss |
Netzanschluss |
400/380 V, 3L/N/PE, 50/60 Hz |
400/380 V, 3L/N/PE, 50/60 Hz |
400/380 V, 3L/N/PE, 50/60 Hz |
Max. Ausgangsstrom |
8,7 A |
14,5 A |
21,7 A |
|
Max. Eingangsstrom |
15,7 A |
26,1 A |
26,1 A |
|
Nominale Scheinleistungsausgabe |
6.000 VA |
10.000 VA |
15.000 VA |
|
Max. Scheinleistungsausgabe |
6.000 VA |
10.000 VA |
15.000 VA |
|
Max. Scheinleistung vom Stromnetz |
7.200 VA |
12.000 VA |
18.000 VA |
|
Cos(φ) |
-0,8 bis +0,8 |
-0,8 bis +0,8 |
-0,8 bis +0,8 |
|
Notstrom |
Notstromfähig |
Ja |
Ja |
Ja |
Netzform |
400/380 V, 3L/N/PE, 50/60 Hz |
400/380 V, 3L/N/PE, 50/60 Hz |
400/380 V, 3L/N/PE, 50/60 Hz |
|
Notstromversorgte Lasten (pro Phase) |
6.000 VA (2.000 VA)* |
10.000 VA (3.333 VA)* |
15.000 VA (5.000 VA)* |
|
Schieflast |
2.000 VA |
3.333 VA |
5.000 VA |
|
Schwarzstart |
Ja |
Ja |
Ja |
|
Solare Nachladung |
Ja |
Ja |
Ja |
|
Wirkungsgrad |
Max. Wirkungsgrad |
98,2 % |
98,2 % |
98,2 % |
Europäischer Wirkungsgrad |
97,2 % |
97,5 % |
97,5 % |
|
Allgemein |
Breite | Tiefe | Höhe |
497 mm | 221 mm | 461 mm |
497 mm | 221 mm | 461 mm |
497 mm | 221 mm | 461 mm |
Gewicht |
23 kg |
25 kg |
25 kg |
|
Topologie |
nicht isoliert |
nicht isoliert |
nicht isoliert |
*also in parallel mains operation
3.3. Technical data — FENECON EMS box
Description | Value/dimension |
---|---|
DC operating voltage |
224 V to 672 V |
Max. current (battery) |
50 A |
Operating temperature |
-10 °C to 50 °C |
Protection specification |
IP55 (plugged) |
Input voltage |
100 V to 240 V/1.8 A/50 Hz to 60 Hz |
Width | Depth | Height |
506 mm | 401 mm | 157 mm |
Weight |
12 kg |
Installation |
stackable |
3.3.2. EMS box — Pin assignment
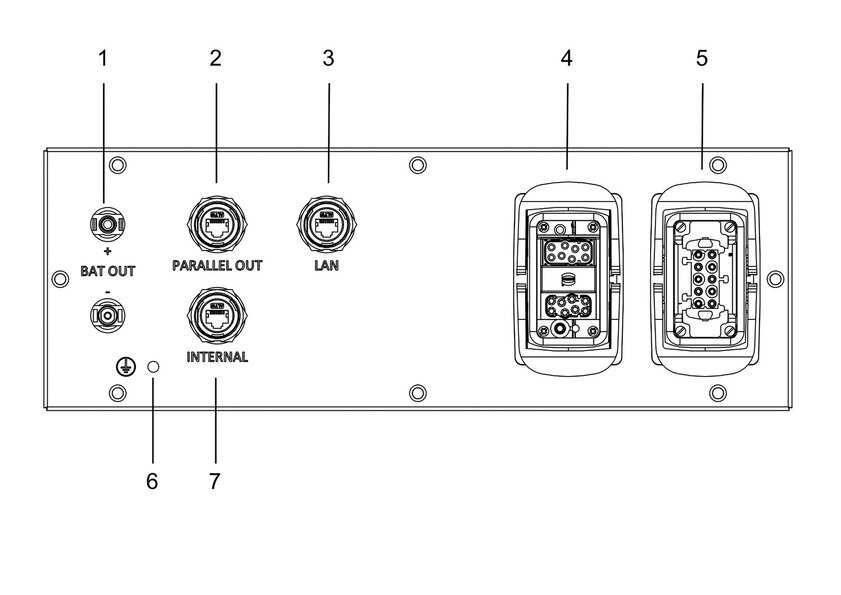
Item | Description |
---|---|
1 |
Battery connection to the inverter (MC4-Evo stor) |
2 |
Communication output for parallel connection of several batteries |
3 |
Customer network connection (LAN) RJ45 (network cable not included) |
4 |
Communication to the inverter, relay outputs; digital inputs (16-pin connector) |
5 |
Power supply FEMS box; potential-free contacts (max. 10 A, measured) (10-pin plug) |
6 |
Earth connection |
7 |
For future applications (not assigned) |
3.4. Technical data — FENECON parallel switch box (optional)
Description | Value/dimension |
---|---|
DC operating voltage |
224 V to 672 V |
Max. current (battery) |
50 A |
Operating temperature |
-10 °C ~ 50 °C |
Protection specification |
IP55 (plugged in) |
Width | Depth | Height |
506 mm |401 mm |157 mm |
Weight |
10 kg |
Installation |
stackable |
3.4.2. Parallel switch box — Terminal assignment
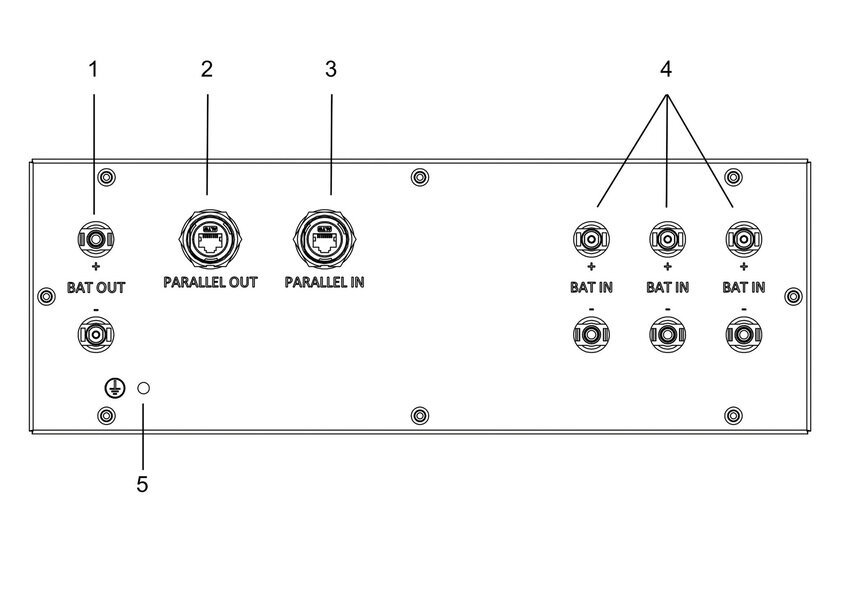
Item | Description |
---|---|
1 |
Battery connection to the inverter (MC4-Evo stor) |
2 |
Communication output for parallel connection of several battery towers |
3 |
Communication input for parallel connection of several battery towers |
4 |
Battery connection for additional battery towers (MC4-Evo stor) |
5 |
Earthing connection |
3.5. Technical data — FENECON Extension box (optional)
Description | Value/dimension |
---|---|
DC operating voltage |
224 V to 672 V |
Max. current (battery) |
50 A |
Operating temperature |
-10 °C ~ 50 °C |
Protection specification |
IP55 (plugged in) |
Width | Depth | Height |
506 mm | 401 mm | 157 mm |
Weight |
9 kg |
Installation |
stackable |
3.5.2. Extension box — Pin assignment
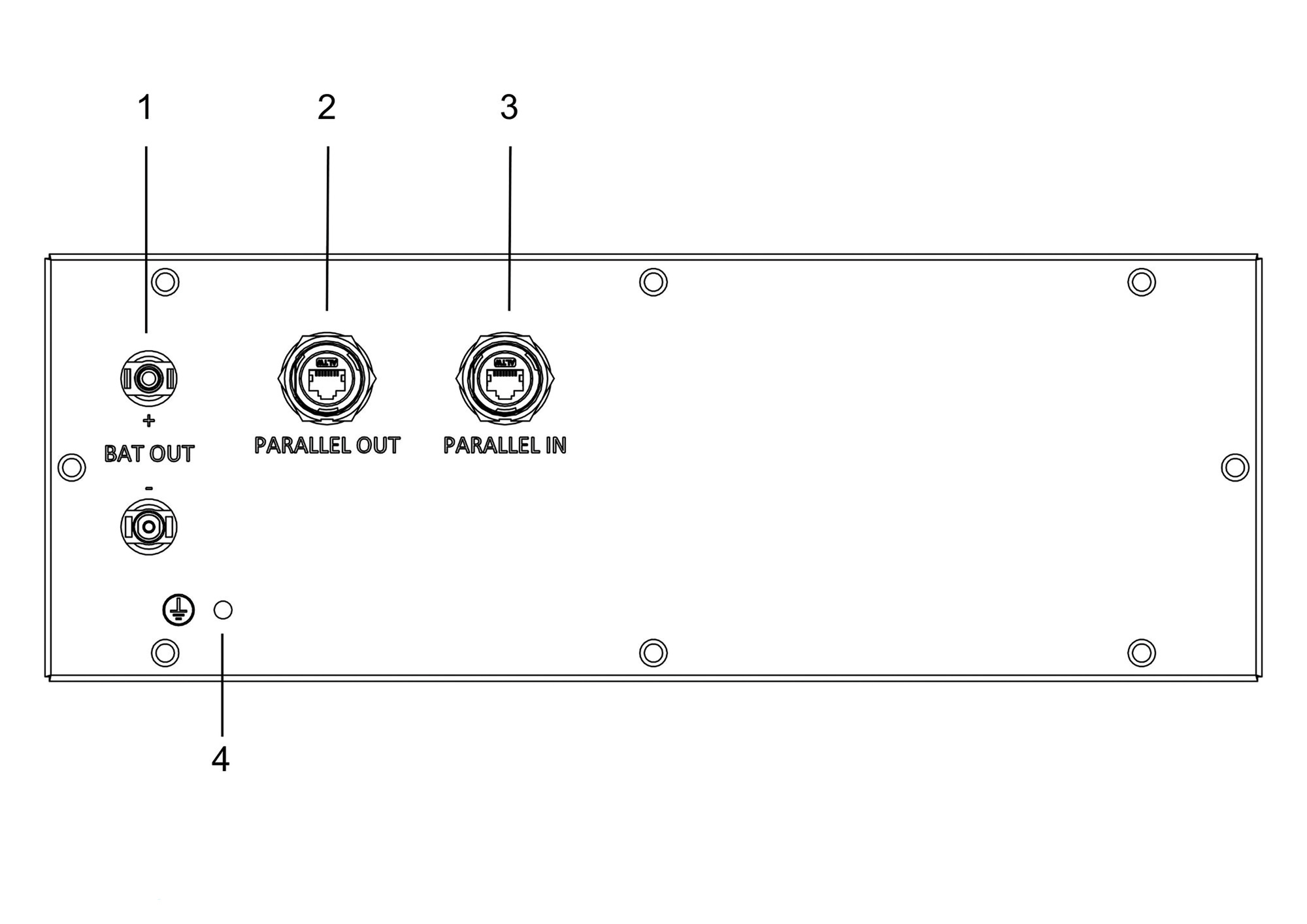
Item | Description |
---|---|
1 |
Battery connection to EMS box in parallel (MC4-Evo stor) |
2 |
Communication output for parallel connection of several battery towers |
3 |
Communication input for parallel connection of several battery towers |
4 |
Earthing connection |
3.6. Technical data — FENECON BMS box
Description | Value/dimension |
---|---|
Maximum operating voltage range |
224 V to 672 V |
Maximum output/input current |
50 A |
Optimal operating temperature |
15 °C to 30 °C |
Operating temperature range |
-20 °C to 55 °C |
Protection specification |
IP55 (plugged in) |
Width (incl. side panel) | Depth | Height |
506 mm |401 mm |143 mm |
Weight |
13 kg |
Installation |
stackable/wall mounting |
3.7. Technische Daten — FENECON-Batteriemodul
Benennung | Wert/Größe |
---|---|
Nutzbare Kapazität |
62,4 Ah/2,80 kWh |
Nennspannung |
44,8 V |
Ausgangsspannungsbereich |
39,2 V bis 50,4 V |
Arbeitstemperatur Batterie |
-20 °C bis +55 °C |
Lagertemperaturbereich (über 7 Tage) |
-30 °C bis +60 °C |
Lagertemperaturbereich (über 30 Tage) |
-20 °C bis +55 °C |
Lagertemperaturbereich (bis 270 Tage kumuliert) |
-10 °C bis +45 °C |
Schutzart |
IP55 (gesteckt) |
Gewicht |
30 kg |
Installation |
stapelbar |
Parallelschaltung |
4 Batterietürme parallel |
Kühlung |
natürliche Kühlung |
Versandkapazität |
< 30 % SoC |
Modul-Sicherheitszertifizierung |
VDE 2510/IEC62619 |
UN-Transportprüfnorm |
UN38.3 |
Relative Luftfeuchtigkeit bei Lagerung |
5 % bis 95 % |
Lagerung länger als 12 Monate
|
3.7.2. Elektrische Parameter der Batteriemodule
Bei Anzahl der Batteriemodule von 3 bis 6
Parameter |
Wert/Größe |
|||
Modulanzahl |
3S* |
4S |
5S |
6S |
Nominale Kapazität |
8,6 kWh |
11,4 kWh |
14,3 kWh |
17,2 kWh |
Breite inkl. Seitenblende |
506 mm |
|||
Tiefe |
401 mm |
|||
Höhe |
834 mm |
977 mm |
1120 mm |
1263 mm |
Gewicht |
127 kg |
157 kg |
187 kg |
217 kg |
Nennspannung |
134,4 V |
179,2 V |
224,0 V |
268,8 V |
Ausgangsspannungsbereich |
117,6 V ~ 151,2 V |
156,8 V ~ 201,6 V |
196 V ~ 252 V |
235,2 V ~ 302,4 V |
Maximale kontinuierliche Lade-/Entladeleistung |
6,72 kW |
8,96 kW |
11,20 kW |
13,44 kW |
Bei Anzahl der Batteriemodule von 8 bis 11
Parameter | Wert/Größe | |||
---|---|---|---|---|
Modul |
8S |
9S |
10S |
11S |
Nominale Kapazität |
22,9 kWh |
25,8 kWh |
28,7 kWh |
31,5 kWh |
Breite inkl. Seitenblende |
506 mm |
|||
Tiefe |
401 mm |
|||
Höhe |
1549 mm |
1692 mm |
1835 mm |
1978 mm |
Gewicht |
277 kg |
307 kg |
337 kg |
367 kg |
Nennspannung |
358,4 V |
403,2 V |
448,0 V |
492,8 V |
Ausgangsspannungsbereich |
313,6 V ~ 403,2 V |
352,8 V ~ 453,6 V |
392,0 V ~ 504,0 V |
431,2 V ~ 554,4 V |
Maximale kontinuierliche Lade-/Entladeleistung |
17,92 kW |
20,16 kW |
22,40 kW |
24,64 kW |
Bei Anzahl der Batteriemodule von 12 bis 14
Parameter | Wert/Größe | ||
---|---|---|---|
Modul |
12S |
13S |
14S |
Nominale Kapazität |
34,4 kWh |
37,3 kWh |
40,1 kWh |
Breite inkl. Seitenblende |
506 mm |
||
Tiefe |
401 mm |
||
Höhe |
2121 mm |
2264 mm |
2407 mm |
Gewicht |
397 kg |
427 kg |
457 kg |
Nennspannung |
537,6 V |
582,4 V |
627,2 V |
Ausgangsspannungsbereich |
470,4 V ~ 604,8 V |
509,6 V ~ 655,2 V |
548,8 V ~ 705,6 V |
Maximale kontinuierliche Lade-/Entladeleistung |
26,88 kW |
29,12 kW |
30,00 kW |
4. General description
FENECON Home 6, 10 & 15 is an emergency-power-capable electrical energy storage system that can build its own household power grid. Lithium iron phosphate batteries (LiFePO4) are used in this modular system for storing electrical energy.
4.1. Explanation of the "emergency power function"
Home 10; Home 6, 10 & 15; Home 20 & 30
The FENECON series hybrid inverter:
-
FHI-10-DAH, FHI-10-DAH 16A, FHI-20-DAH, FHI-29,9-DAH
-
FINV-6-2-DAH, FINV-10-2-DAH, FINV-15-2-DAH
has an additional output for consumer loads with emergency power capability. In the event of a mains failure, the inverter disconnects the two outputs from each other at all poles, with N and PE being bridged at the emergency power output. The entire switching pattern in less than 10 ms is integrated in the inverter.
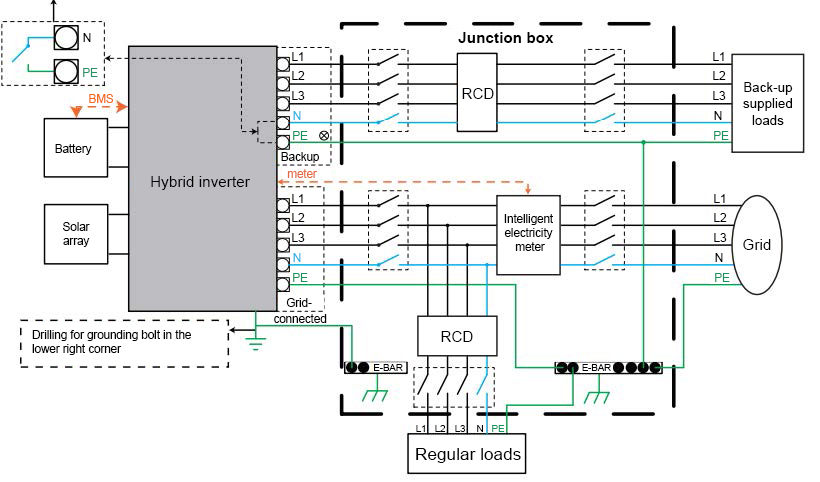
The emergency power grid is a genuine three-phase current with 100 % unbalanced load capability and a slightly increased frequency for simple synchronization when the grid returns. If the voltage is equal on all phases when the grid is restored, the switchover to parallel mains operation takes place again within a few milliseconds. The emergency power supply can only be maintained if the state of charge of the battery is sufficient. If this is not the case, the battery is charged from the connected PV strings before the emergency power grid can be black-started.
4.2. System configuration — General overview
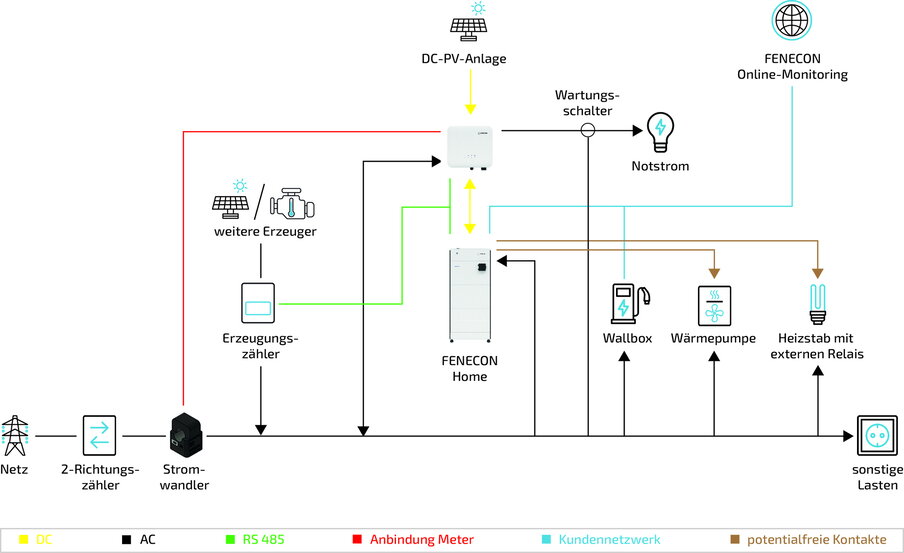
4.3. System structure: Variants with emergency power
4.3.1. Standard setup with emergency power
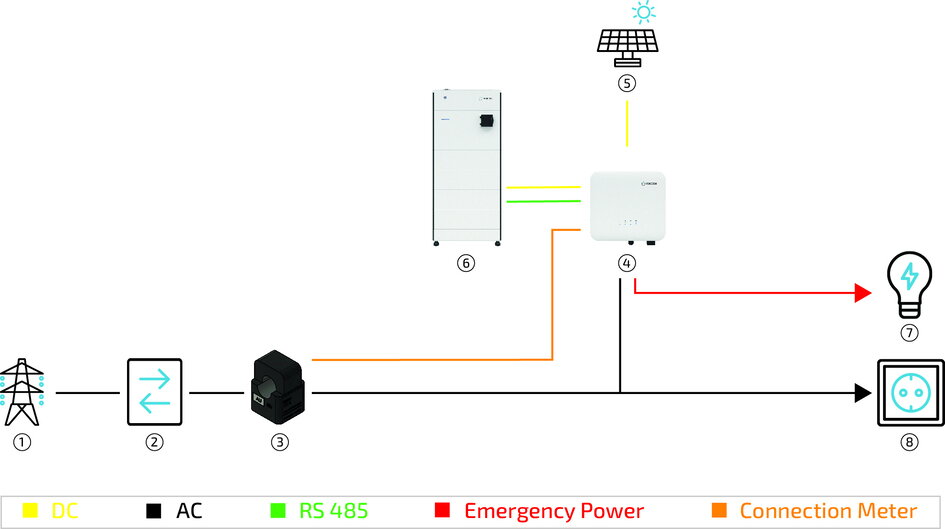
Item | Description |
---|---|
1 |
Grid |
2 |
Bi-directional meter |
3 |
Current transformer |
4 |
Inverter |
5 |
PV system |
6 |
Electrical energy storage |
7 |
Load(s) (supplied with emergency power) |
8 |
Load(s) (not supplied with emergency power) |
Within the emergency power function, the inverter acts as its own grid former and sets up its own 3-phase system for the separate emergency power branch (see Technical data). Compared to the public grid system, the grid shape of the emergency power mode has a lower "buffer effect" with regard to load peaks, starting currents, DC components and strongly fluctuating loads. Due to the limited power of the inverter, such loads are only possible within certain limits. The manufacturer is not responsible for the domestic installation. |
4.3.2. System structure with additional PV generator
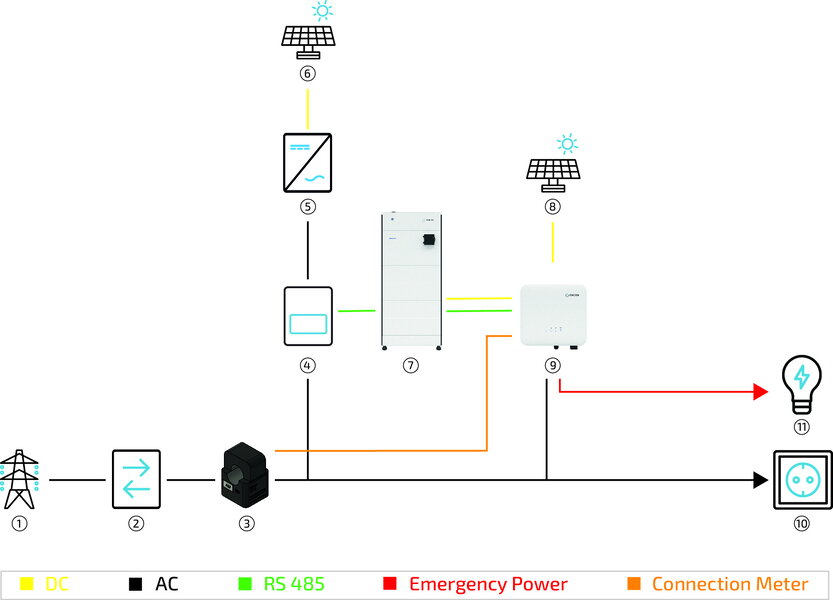
Item | Description |
---|---|
1 |
Grid |
2 |
Bi-directional meter |
3 |
Current transformer |
4 |
3-phase sensor or with PV-Inverter app |
5 |
PV inverter |
6 |
Additional PV system |
7 |
Electrical energy storage |
8 |
PV system |
9 |
Inverter |
10 |
Load(s) (supplied with emergency power) |
11 |
Load(s) (not supplied with emergency power) |
4.3.3. System structure as an AC system
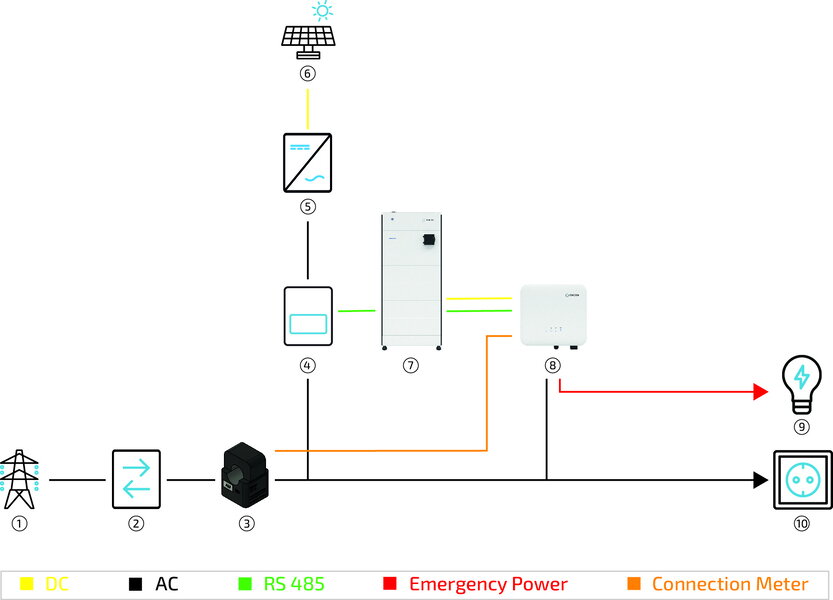
Item | Description |
---|---|
1 |
Grid |
2 |
Bi-directional meter |
3 |
Current transformer |
4 |
3-phase sensor or with PV Inverter app |
5 |
PV inverter |
6 |
PV system |
7 |
Electrical energy storage |
8 |
Inverter |
9 |
Load(s) (supplied with emergency power) |
10 |
Load(s) (not supplied with emergency power) |
4.3.4. System with manual emergency power changeover
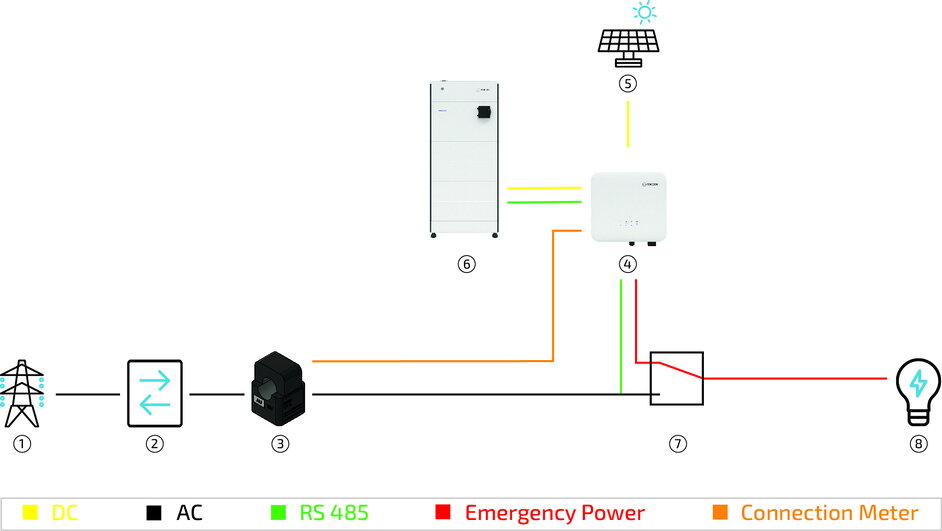
Item | Description |
---|---|
1 |
Grid |
2 |
Bi-directional meter |
3 |
Current transformer |
4 |
Inverter |
5 |
PV system |
6 |
Electrical energy storage |
7 |
Manual emergency power switch |
8 |
Load(s) (supplied with emergency power) |
4.3.5. System setup with automatic off-grid switch (FENECON AVU) — FENECON Home 6 & 10
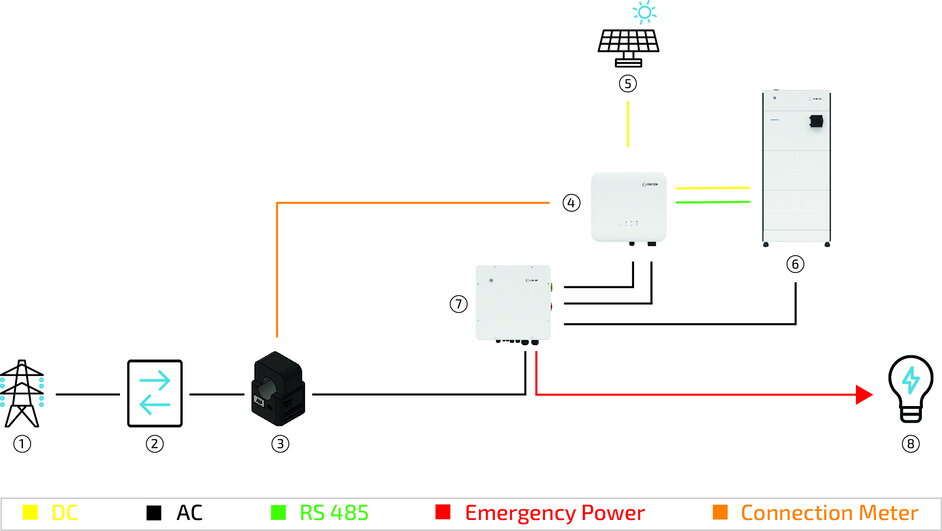
Item | Description |
---|---|
1 |
Grid |
2 |
Bi-directional meter |
3 |
Smartmeter |
4 |
Inverter |
5 |
PV system |
6 |
FENECON Home 6 or Home 10 |
7 |
Automatic off-grid switch (AVU) * |
8 |
Consumer load |
*For installing the automatic off-grid switch, use the associated assembly and operating instructions. These can be found on the FENECON website in the download center at: https://fenecon.de/files-avu/.
The automatic off-grid switch is only compatible with Home 6 and Home 10 systems. |
4.3.6. Required components
Depending on the system configuration, a maximum of the following components is required. When connecting up to four battery towers in parallel, ensure that the same number of battery modules is installed in each battery tower.
Number of battery towers |
Number of battery modules max. |
BMS box |
EMS box |
Parallel switch box |
Extension box |
1 |
14 |
1 |
1 |
- |
- |
2 |
28 |
1 |
1 |
1 |
- |
3 |
42 |
1 |
1 |
1 |
1 |
4 |
56 |
1 |
1 |
1 |
2 |
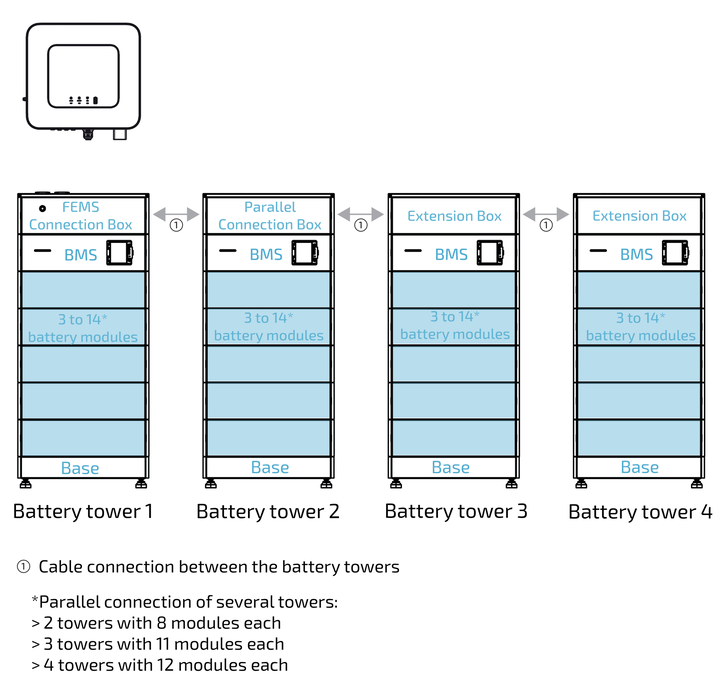
5. Assembly preparation
5.1. Scope of delivery
5.1.1. FENECON Home 6, 10 & 15-Inverter — Variants A & B
There are two variants of the inverter in circulation. The functions and technical data of the two variants are exactly the same. The junction box of the communication lines and the current transformers differ minimally. For this reason, the instructions in the relevant sections always list a Variant A and a Variant B. |
Illustration | Amount | Description |
---|---|---|
![]() |
1 |
FENECON Home 6, 10 & 15-Inverter |
![]() |
2 |
Tools for PV and battery plugs |
![]() |
1 |
Wall mount |
![]() |
1 |
Split-core CT communication cable |
![]() |
3 |
Split-core CT |
![]() |
1 |
Communication port cover |
![]() |
2(3) |
MC4 plug |
![]() |
2(3) |
MC4 socket |
![]() |
1 |
FEMS-Cable |
![]() |
1 |
2-Pin Push-In-Connector |
1 |
4-Pin Push-In-Connector |
|
2 |
6-Pin Push-In-Connector |
|
![]() |
1 |
PE cable lug |
![]() |
4 |
Screw with screw anchor |
![]() |
1 |
Cover AC connection |
![]() |
1 |
M5 bolt for earthing |
Illustration | Amount | Description |
---|---|---|
![]() |
1 |
FENECON Home 6, 10 & 15-Inverter |
![]() |
2 |
Tools for PV and battery plugs |
![]() |
1 |
Wall mount |
![]() |
1 |
Split-core CT |
![]() |
1 |
Cover communication port |
![]() |
2(3) |
MC4 plug |
![]() |
2(3) |
MC4 socket |
![]() |
1 |
FEMS-Cable |
![]() |
1 |
2-Pin-Push-In-Connector |
3 |
4-Pin-Push-In-Connector |
|
1 |
6-pin push-in connector |
|
![]() |
1 |
PE cable lug |
![]() |
4 |
Screw with screw anchor |
![]() |
1 |
Cover AC connection |
![]() |
1 |
M5 bolt for earthing |
5.1.2. FENECON EMS box
Illustration | Amount | Description |
---|---|---|
![]() |
1 |
FENECON-EMS box |
![]() |
2 |
Side panel |
![]() |
2 |
Harting housing with cable gland 13-21 mm, multi-hole seal 4 x 8mm |
![]() |
1 |
Harting socket 10-pin |
![]() |
1 |
Harting insert 16-pin (assembled) |
![]() |
1 |
Jumper plug |
![]() |
2 |
Network connector housing |
![]() |
5 |
Filler plug, 8 mm |
![]() |
2 |
Filler plug, 10 mm |
![]() |
1 |
Battery cable set, 3 m |
![]() |
1 |
Installation and service instructions (QR code) |
![]() |
1 |
Operating instructions (for the end customer, |
![]() |
1 |
Quick start guide |
5.1.3. FENECON parallel switch box (optional)
Illustration | Amount | Description |
---|---|---|
![]() |
1 |
FENECON-Parallel switch box |
![]() |
2 |
Side panel |
![]() |
2 |
Each set of two DC cables, 2 m |
![]() |
1 |
Communication cable parallel connection, 2 m |
5.1.4. FENECON — Extension box (optional)
Illustration | Amount | Description |
---|---|---|
![]() |
1 |
FENECON-Extension box |
![]() |
2 |
Side panel |
![]() |
2 |
each set of two DC cables, 2 m |
![]() |
1 |
Communication cable, 2 m |
5.2. Tools required
The following tools/machines are required for assembling the system components:
Illustration | Description | Illustration | Description |
---|---|---|---|
![]() |
Pencil |
![]() |
Spirit level |
![]() |
Impact drill or |
![]() |
Screwdriver set |
![]() |
Meter stick |
![]() |
Side cutter |
![]() |
Allen key, 3 mm |
![]() |
Set of flat spanners |
![]() |
Crimping tool |
![]() |
Multimeter |
![]() |
Pliers for cable glands |
![]() |
Protective eyewear |
![]() |
Protective footwear |
![]() |
Dust mask |
![]() |
Rubber mallet |
![]() |
Vacuum cleaner |
![]() |
Wire stripper |
![]() |
Protective gloves |
![]() |
Torque wrench |
![]() |
Insulation stripping knife |
6. Assembly
|
|
|
Suitable protective covers must be fitted! |
The following components must be installed:
-
Inverter
-
Battery tower with base, battery modules, BMS box and FENECON EMS box
-
Optional:
-
Battery tower with base, battery modules, BMS box and parallel switch box
-
-
Optional:
-
Battery tower with Base, battery modules, BMS Box and Extension Box
-
Before installation, carefully check whether the packaging and products are damaged and whether all accessories listed in the Scope of delivery section are included. If a part is missing or damaged, contact the manufacturer/dealer.
6.1. Assembly Inverter
6.1.1. Safety instructions
Electric shock from live parts
|
Electric shock in the absence of overvoltage protection
|
Fire and explosion
|
Fire and explosion hazard with deeply discharged battery modules
|
Toxic substances, gases and dusts
|
Arcing due to short-circuit currents
|
Destruction of a measuring device due to overvoltage
|
Hot surfaces
|
Weight of the inverter
|
Sand, dust and moisture |
Electrostatic charge
|
Cleaning agents
|
6.1.2. Installation conditions and distances at the installation site
Indoor or outdoor installation
We recommend installing the FENECON Home 6, 10 & 15 battery towers in a well-ventilated room without external heat sources. However, the battery tower(s) can also be installed outdoors protected from the weather (e. g. garage).
Installation at and above 2000 m above sea level and in unventilated locations is not permitted.
Also unauthorized installation locations:
-
those with an explosive atmosphere.
-
Places where flammable or oxidizing substances are stored.
-
Wet rooms.
-
places where salty moisture, ammonia, corrosive vapors or acid can ingress into the system.
The storage system should also be inaccessible to children and animals.
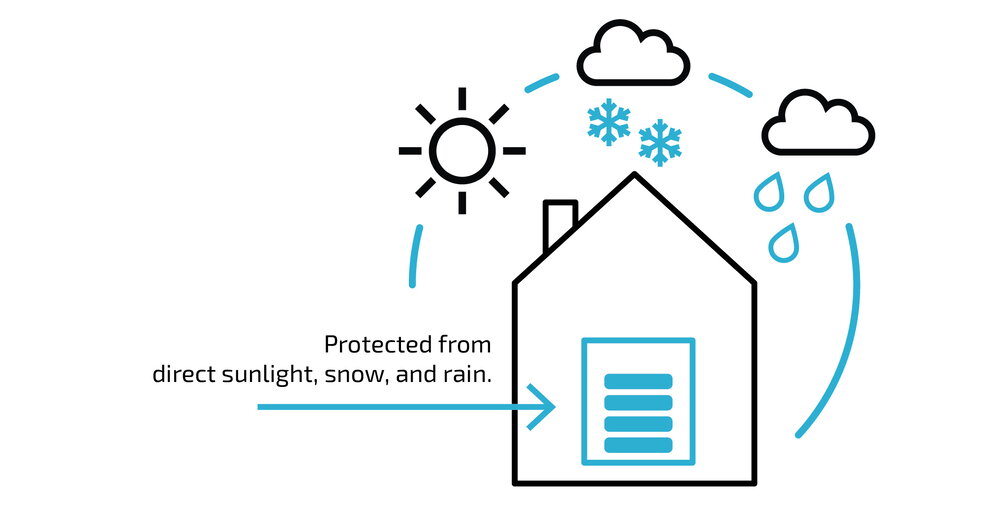
-
The inverter must be installed protected from direct sunlight, rain and snow.
-
In conditions outside the optimum temperature range, the performance of the batteries is reduced. (optimum temperature range: +15 °C to +30 °C)
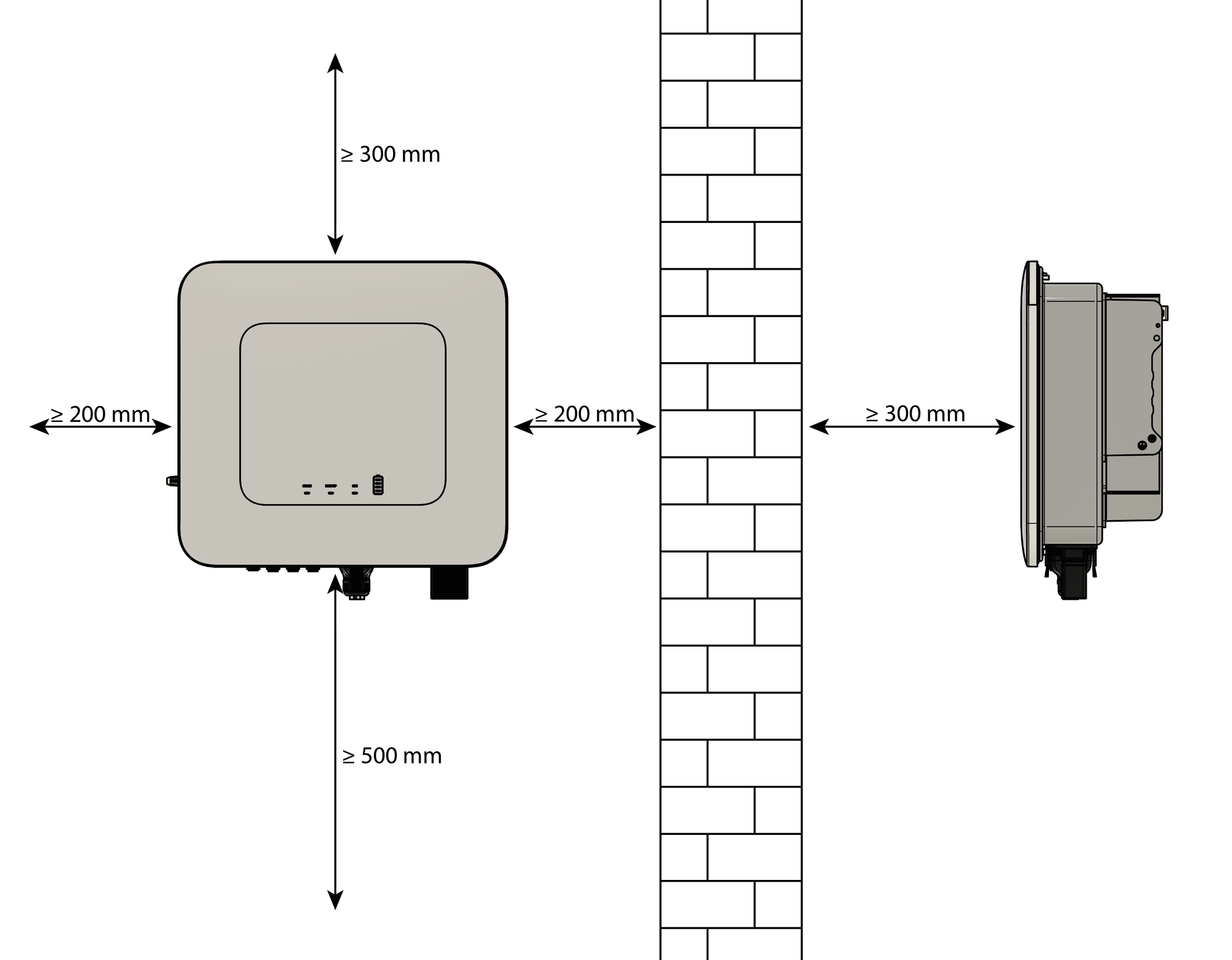
Installation conditions
|
6.1.3. Assembly
To install the FENECON Home 6, 10 & 15 inverter on the wall, proceed as follows:
Assembly of the wall bracket
![]() |
|
![]() |
|
![]() |
|
![]() |
|
6.2. Assembly of battery tower 1 with FEMS box
6.2.1. Safety instructions
Electric shock from live parts
|
Electric shock in the absence of overvoltage protection
|
Fire and explosion
|
Fire and explosion if battery modules are deeply discharged
|
Toxic substances, gases and dusts
|
Arcing due to short-circuit currents
|
Destruction of a measuring device due to overvoltage
|
Hot surfaces
|
Weight of the battery modules
|
Sand, dust and moisture
|
Electrostatic charging
|
Cleaning agents
|
Place of installation
|
Installation
|
6.2.2. Conditions at the installation site
Indoor or outdoor installation
We recommend installing the FENECON Home 6, 10 & 15 battery tower indoors. However, the battery tower can also be installed outdoors protected from the weather (e. g. garage).
6.2.3. Installation conditions and distances at the installation site
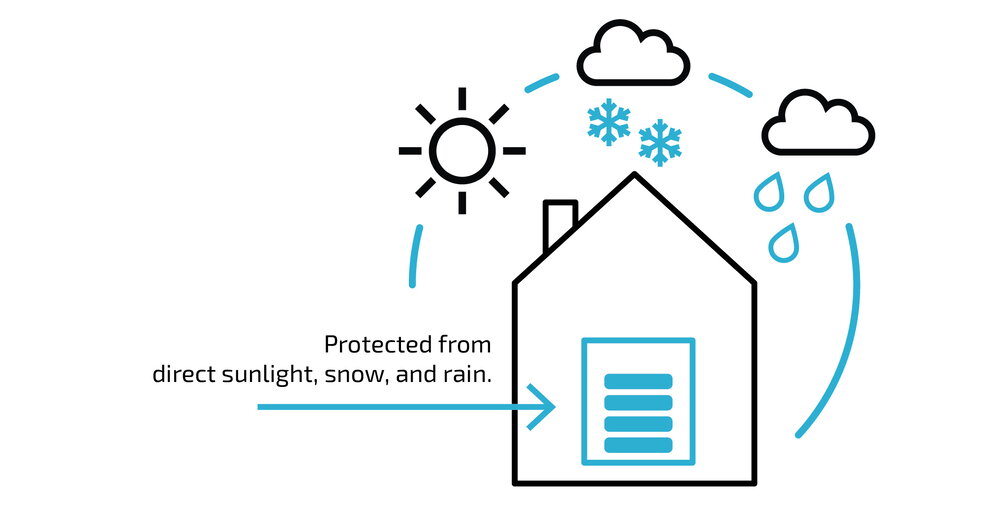
-
The battery tower must be installed protected from direct sunlight, rain and snow.
-
In conditions outside the optimum temperature range, the performance of the battery is reduced. (optimum temperature range +15 °C to +30 °C)
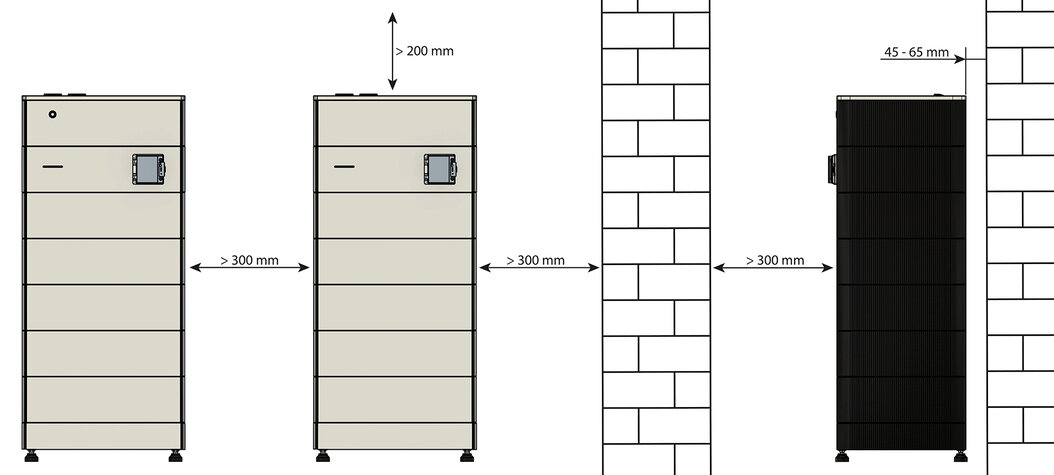
-
Empfohlen wird ein seitlicher Abstand von 300 mm von einer Wand und 300 mm zwischen zwei Batterietürmen.
-
Auf der Vorderseite werden 300 mm Abstand von einer Wand empfohlen.
-
The FENECON Home 6, 10 & 15 battery tower and inverter should be installed/mounted on top of each other. If there is not enough space above, the battery tower and inverter can also be installed next to each other.
-
A distance of 200 mm from the ceiling is recommended.
If the recommended distances are not observed, installation may be more difficult and derating may occur earlier. |
6.2.4. Assembly of battery tower 1 with FENECON EMS box
Proceed as follows to set up the battery tower:
![]() |
|
![]() |
|
![]() |
|
Stack a maximum of 14 FENECON battery modules on one base. |
![]() |
|
Electric shock
|
![]() |
|
![]() |
|
![]() |
|
![]() |
|
![]() |
|

You will find the installation instructions for 2 or 3 battery towers in the section Electrical installation of additional battery towers. |
6.3. Electrical installation
6.3.1. Earthing the inverter and the battery tower
![]() |
|
![]() |
|
![]() |
|
The grounding cable requires a cross-section of at least 10 mm2. |
6.4. Approved grid shapes for connecting the FENECON Home 6, 10 & 15
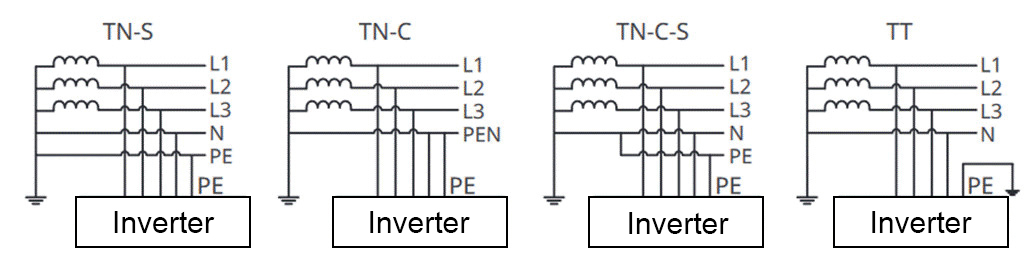
6.4.1. Connection and wiring of the AC circuit
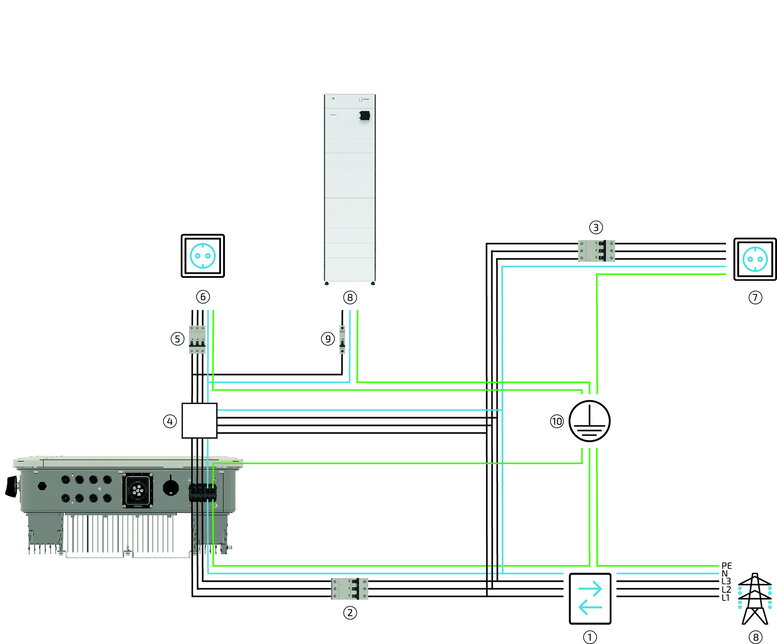
List item | Description |
---|---|
1 |
Bi-directional meter from the energy supplier |
2 |
3-pole inverter fuse protection (6 kW — 20 A; 10/15 kW — 32 A).* |
3 |
Fuse protection of the consumer loads (no emergency power) with RCD type A and suitable MCBs. |
4 |
Service switch for switching the emergency power loads to the mains (recommended). |
5 |
Consumer loads protected by suitable MCBs and RCD type A 30 mA.** |
6 |
Consumer loads — emergency power supply maximum 6/10/15 kW — 2 kW/3.333kW/5 kW per phase (also applies in normal operation if grid available!); no other AC generators permitted |
7 |
Consumer loads (not supplied with emergency power) |
8 |
AC supply of the EMS box (if consumer loads are connected to the emergency power outlet). |
9 |
Fuse protection maximum C6 or C10 1-pole. |
10 |
Earth circuit connector |
* In addition, the currently valid national regulations and the specifications of the relevant grid operator must be observed. (If an RCD is required by the grid operator, an RCD type A with a tripping current of 300 mA is recommended; at 30 mA, unwanted shutdowns may occur).
** The currently valid national regulations, the specifications of the relevant network operator and the manufacturer’s specifications must be observed.
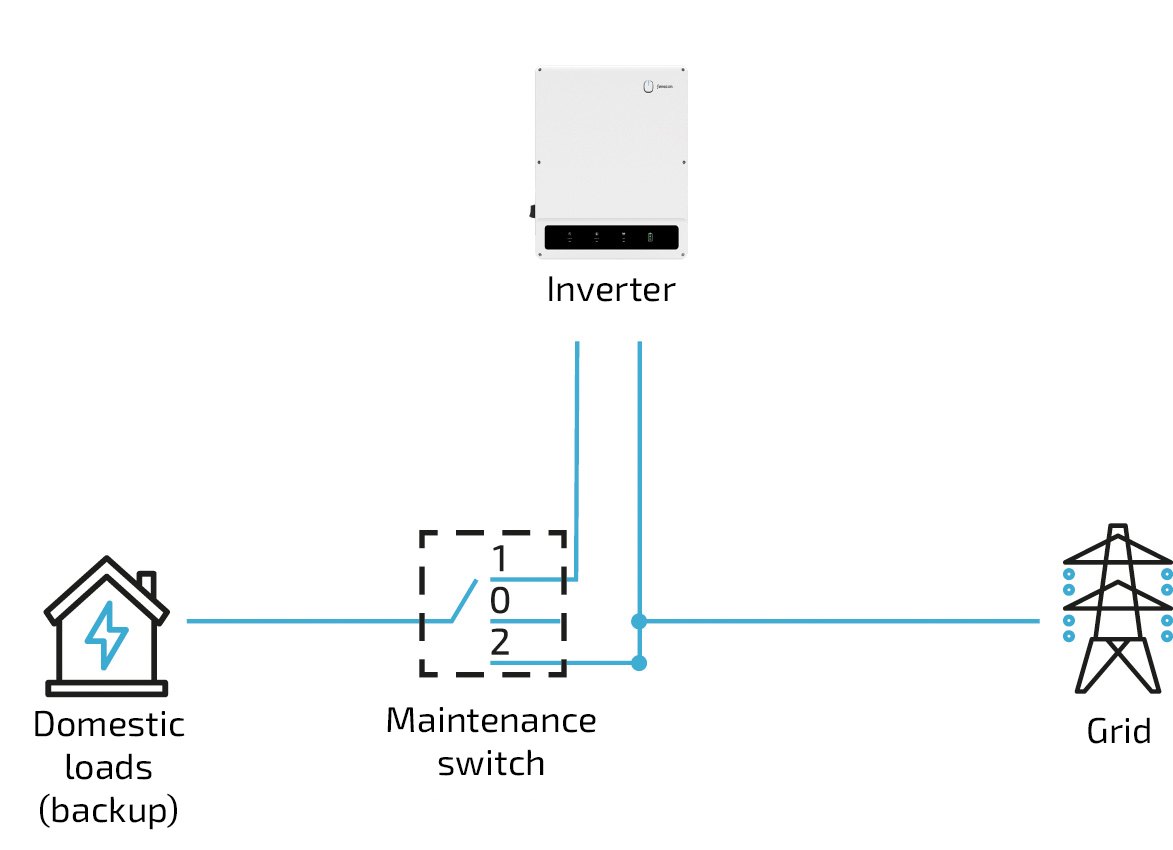
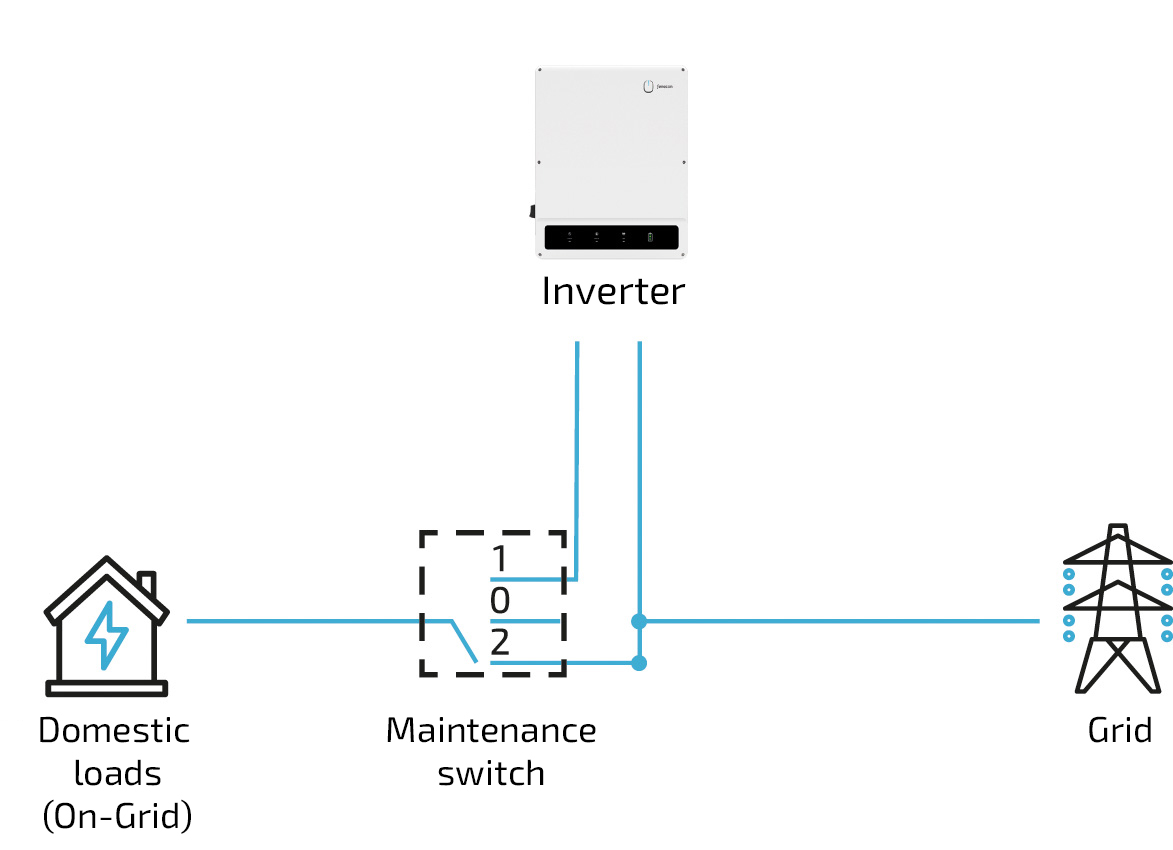
List item | Description |
---|---|
1 |
Emergency power consumers are supplied with emergency power via inverter (normal position) |
2 |
Emergency power consumers are disconnected from the inverter and grid |
3 |
Emergency power consumers are supplied from the grid |
The automatic emergency power switchover is not affected by the maintenance switch. |
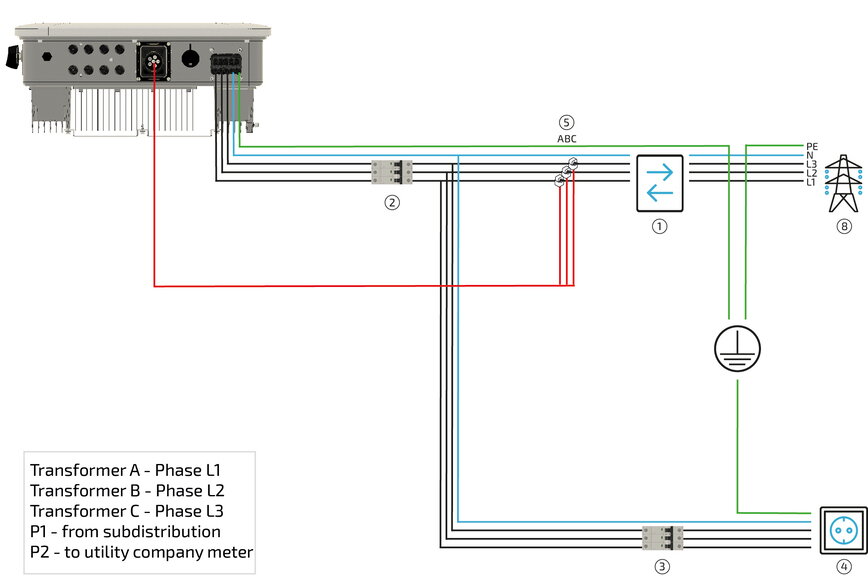
List item |
Description |
1 |
Bi-directional meter from energy supplier |
2 |
Inverter fuse protection C20/C32 3-pole* |
3 |
Fuse protection of the consumer loads (no emergency power) with RCD type A and suitable MCBs |
4 |
Consumer loads, not supplied with emergency power |
5 |
Split-core CT (directly behind grid operator meter) Connection to inverter |
* In addition, the currently valid national regulations and the specifications of the relevant grid operator must be observed. (If an RCD is required by the grid operator, an RCD type A with a tripping current of 300 mA is recommended; at 30 mA, unwanted shutdowns may occur).
![]() |
|
![]() |
|
||
Section |
Description |
Dimensions |
|
1 |
Outer diameter |
18 mm |
|
2 |
Length stripped |
BACKUP: 75 mm |
|
3 |
Length of stripped conductor |
approx. 12 mm2 * |
|
4 |
Conductor cross-section |
Home 6: 2,5 mm2 * |
|
![]() |
|
||
![]() |
|
||
![]() |
|
*Select the cable cross-section, fuse type and fuse value according to the following general conditions: Country-specific installation standards, power class of the device, cable length, type of cable routing, local temperatures
If flexible conductors are involved, wire ferrules must be used accordingly.
A 4-pole maintenance switch is recommended. Care must be taken to ensure that no neutral displacement can occur during switching. The correct maintenance switch must be selected by a specialist company, taking into account the conditions on site. |
6.4.2. AC connection of the FENECON EMS box
An external 230-V-power-supply is required to supply the FENECON EMS box.
The purpose of this is to avoid loading the empty battery with additional consumer loads. This can occur particularly in winter when there is no sunshine or when there is snow on the PV system.
![]() |
|
![]() |
|
![]() |
|
![]() |
|
![]() |
|
6.5. Explanation of the "zero feed-in" function
Anschluss und Betrieb von Speichern am Niederspannungsnetz gemäß VDE-FNN Hinweis 07/2024 — Anforderungen an den Energiefluss-Richtungssensor EnFluRi (Kapitel 4.3) und Nulleinspeiser (Kapitel 4.4).
Die FENECON GmbH erklärt hiermit, dass die in der folgenden Tabelle aufgeführten Wechselrichter in Kombination mit den jeweils angegebenen Energiezählern obige Anforderungen erfüllen:
Wechselrichter |
Bezeichnung |
Internes Energy Meter |
Home Energy Meter |
3-Phasensensor ohne Stromwandler |
---|---|---|---|---|
Home 6 |
FINV-6-2-DAH |
(optional) |
||
Home 10 (Gen. 1) |
FHI-10-DAH |
|||
Home 10 (Gen. 1) |
FHI-10-DAH 16A |
|||
Home 10 |
FINV-10-2-DAH |
(optional) |
||
Home 15 |
FINV-15-2-DAH |
(optional) |
||
Home 20 |
FHI-20-DAH |
(optional) |
||
Home 30 |
FHI-29,9-DAH |
(optional) |
||
Commercial 50 (Gen. 3) |
FINV-50-1-DAH |
6.5.1. Konfiguration zur Nulleinspeisung über das FENECON Energy Management System
Die oben aufgeführten Wechselrichter können über das FENECON Energy Management System so konfiguriert werden, dass die erzeugte PV-Energie vollständig selbst genutzt und keine Einspeisung in das öffentliche Netz erfolgt.
Hierzu ist die Einstellung Maximale Einspeiseleistung im Inbetriebnahme-Assistenten auf 0 Watt festzulegen.
6.5.2. Hinweise zur Nulleinspeisefunktion:
-
Bei Verwendung von FENECON-Wechselrichtern kann es zu Abweichungen von < 1 % pro Phase kommen.
-
Die Genauigkeit der Nulleinspeisung ist abhängig vom Leistungsfaktor der angeschlossenen Verbraucher.
-
Ein hoher Anteil an Blindleistung, insbesondere in Form von Oberschwingungen, kann die Genauigkeit der Messung der Wirkleistung negativ beeinflussen.
6.5.3. Gültigkeit der Erklärung:
Diese Erklärung gilt für alle baugleichen Exemplare der genannten Wechselrichter. Sie verliert ihre Gültigkeit, wenn:
-
Änderungen am Gerät vorgenommen wurden,
-
der Anschluss unsachgemäß erfolgt,
-
die Installation nicht gemäß der Betriebsanleitung durchgeführt wurde, oder
-
der Wechselrichter mit einem externen Erzeuger betrieben wird.
6.5.4. DC cable from the battery tower to the Inverter
This section can be skipped if there are several battery towers.
You will find the installation instructions for 2 or 3 battery towers in the section Electrical installation of additional battery towers. |
![]() |
|
The DC plugs used on the battery side are not compatible with commercially available MC4 plugs. |
6.5.5. Connection and cabling of PV system
![]() |
The various PV strings can be connected directly to the PV inputs on the inverter. The 6 kW variant has 2 MPPTs, each with one input (red; blue). For the 10 kW and 15 kW variants, 3 MPPTs are available, each with one input (red; blue; green) |
![]() |
Type 2 overvoltage protection is integrated in the inverter. |
6.5.6. Communication between inverter and EMS box
![]() |
|
![]() |
Variant A
|
![]() |
Variant B
|
![]() |
|
![]() |
|
![]() |
|
![]() |
|
If controllable consumer loads have been installed and one of the following FEMS extensions has been purchased, the following two steps can be neglected for the time being.
|
![]() |
|
![]() |
|
6.5.7. Communication from a battery tower
![]() |
If only one battery tower is installed, the jumper plug (included) must be plugged into the PARALLEL OUT connection and locked by turning the underside. |
You will find the installation instructions for 2 or 3 battery towers in the section Electrical installation of additional battery towers. |
6.5.8. Communication with the customer network
![]() |
|
If the battery tower is installed indoors, this point can be skipped and the network cable can be connected directly. |
![]() |
|
![]() |
|
The electrical energy storage system does not offer WiFi functionality. |
6.6. Connection and wiring of the system’s measuring device
6.6.1. Standard split-core CT
Three split-core CTs with a 10 m long cable are included with the system as standard. No additional measuring device needs to be installed in the meter cabinet. The required voltage data is measured directly at the inverter.
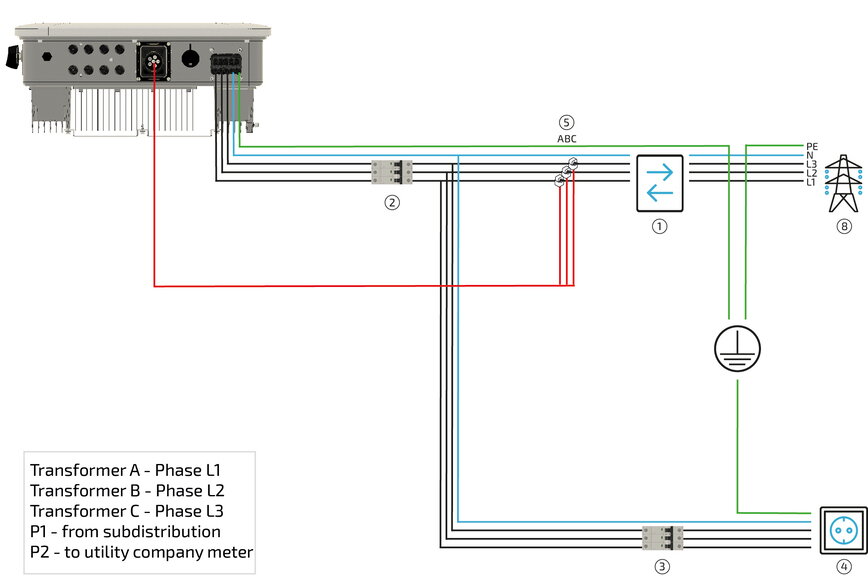
List item | Description |
---|---|
1 |
Bi-directional meter from energy supplier |
2 |
Inverter fuse protection C20/C32 3-pole* |
3 |
Fuse protection of the consumer loads (no emergency power) with RCD type A and suitable MCBs |
4 |
Consumer loads not supplied with emergency power |
5 |
Split-core CT (directly behind grid operator meter), connection to inverter |
In addition, the currently valid national regulations and the specifications of the relevant grid operator must be observed. (If an RCD is required by the grid operator, an RCD type A with a tripping current of 300 mA is recommended; at 30 mA, unwanted shutdowns may occur). |
6.6.2. Connection — Split-core CT variant A
![]() |
|
![]() |
|
![]() |
|
![]() |
|
6.6.3. Connection — Split-core CT variant B
For variant B, a network cable (min. CAT5e) of the appropriate length is required. |
![]() |
|
![]() |
|
![]() |
|
![]() |
|
The maximum current carrying capacity is 120 A per phase. |
6.6.4. Optional split-core CTs with external measuring device
If the cable (10 m) of the standard split-core CTs is too short, an external measuring device with already connected split-core CTs can be installed as an option. A maximum cable length of 100 m is possible between the measuring device and the inverter.
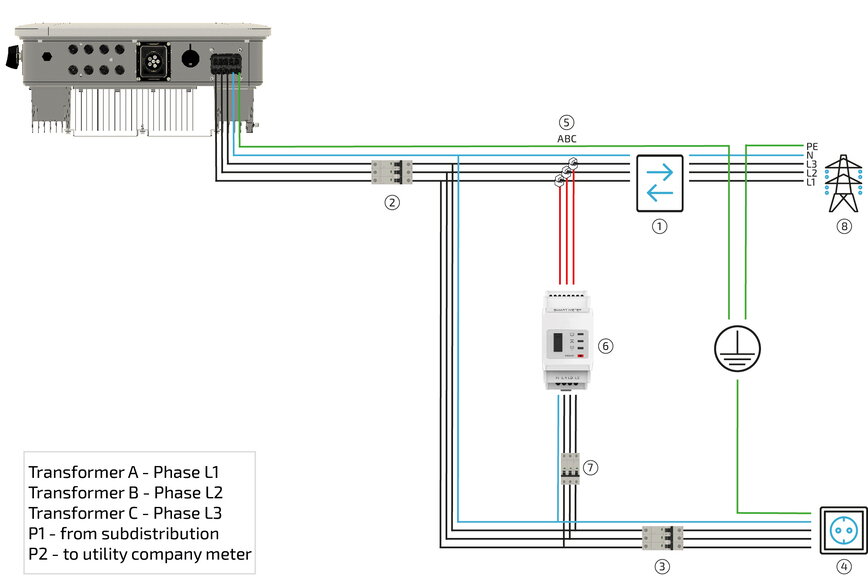
List item | Description |
---|---|
1 |
Bi-directional meter from energy supplier |
2 |
Inverter fuse protection C20/C32 3-pole* |
3 |
Fuse protection of the consumer loads (no emergency power) with RCD type A and suitable MCBs |
4 |
Consumer loads not supplied with emergency power |
5 |
Split-core CT (directly behind grid operator meter), connection to inverter |
6 |
Energy meter |
7 |
Fuse protection of the energy meter (recommended) B6 3-pole |
In addition, the currently valid national regulations and the specifications of the relevant grid operator must be observed. (If an RCD is required by the grid operator, an RCD type A with a tripping current of 300 mA is recommended; at 30 mA, unwanted shutdowns may occur). |
![]() |
|
![]() |
|
![]() |
A standard CAT6 network cable or installation cable with crimped-on plug can be used for the following step.
|
![]() |
|
![]() |
Variante A
|
![]() |
Variant B
|
![]() |
|
The maximum current carrying capacity is 120 A per phase. |
6.6.5. Plugging the internal input (optional)
![]() |
Optionally, a network connector housing with filler plug (included in the scope of delivery) can be used as a cover for the internal connection. |
An IP classification is only guaranteed if the corresponding plugs are locked at all connections. |
7. Parallel connection of several battery towers
7.1. Assembly of further battery towers
7.1.1. Assembly of battery tower 2 with FENECON parallel switch box
If a second battery tower is available, the parallel switch box is plugged onto the second battery tower instead of the EMS box.
![]() |
To do this, repeat the steps from the section Assembly of battery tower 1 with FENECON EMS box. In step 8, attach the FENECON parallel switch box instead of the FENECON EMS box. |
7.1.2. Assembly of battery tower(s) 3 to 4 with FENECON Extension box
If there is a third to fourth battery tower, an Extension box is attached to the third to fourth battery tower instead of the EMS box.
![]() |
To do this, repeat the steps from the section Assembly of battery tower 1 with FENECON EMS box. In step 8, attach the FENECON extension box instead of the FENECON EMS box. |
7.2. Electrical installation of additional battery towers
7.2.1. DC cable between two battery towers and the Inverter
![]() |
|
7.2.2. DC cable between the third to fourth battery tower and parallel switch box
![]() |
|
7.3. Communication of further battery towers
7.3.1. Communication between two to four battery towers
![]() |
|
8. Initial commissioning
8.1. Checking the installation, connections and cabling
Check the system as follows before initial commissioning:
-
All components (distances, environment, mounting) are installed correctly.
-
All internal wiring is complete and properly connected.
-
All external supply lines (power supply, communication cable) are properly connected.
-
All connected loads are matched to the system and the necessary settings have been made.
-
All necessary tests of the system were carried out in accordance with the standards.
Commissioning must only be carried out by trained specialist personnel. |
|
This is indicated in the installation and service instructions:
|
8.2. Switching the system on/off
8.2.1. Switching on the system
![]() |
|
![]() |
|
![]() |
|
The system is restarted by pressing the push-button on the front of the EMS box. Restarting the system can take up to three minutes. |
If the system has not yet been configured, the battery goes into error mode or switches off. The inverter only starts after configuration and only then synchronizes with the grid. |
8.2.2. Switching off the system
![]() |
|
![]() |
|
![]() |
|
8.3. Configuration via commissioning wizard
Open the FENECON homepage and click on the login for FEMS Online Monitoring "FEMS login" in the top right-hand corner. Alternatively, you can use the following QR code or link to access the page.
![]() |
|
![]() |
|
![]() |
|
![]() |
|
![]() |
|
![]() |
|
![]() |
|
|
9. FEMS Online Monitoring
The FEMS Online Monitoring is used to visualize all energy flows in your system. The energy monitor shows live data on grid withdrawal or feed-in, PV production, charging/discharging of the battery storage system and electricity consumption. Other widgets display the percentage of self-sufficiency and self-consumption. In addition, the individual widgets offer a detailed view, which can also be used to view the performance values with phase accuracy.
In addition to the pure information display, all additionally purchased FEMS extensions, such as for integrating a heat pump, Heating element, combined heat and power plant (CHP), are also listed in Online Monitoring. Their functionality can be controlled via the corresponding widget.
In addition to the live view, the history offers the option of selecting self-selected time periods for Online Monitoring. The status of the entire system and the individual components can be monitored at any time using the info symbol.
9.1. Login data
Access to FEMS Online Monitoring is separated according to end customer and installer.
9.1.1. Access for the end customer
Access for the end customer is generated automatically after commissioning is complete and sent to the end customer by email.
The terms and conditions still need to be confirmed here, then the monitoring is available without restrictions.
If additional users want to access the system, they must create their own user account. This is done as described in the section Configuration via commissioning wizard, but here "USER" must be selected in the header.
After successfully creating an additional user account, all we need is an e-mail to service@fenecon.de with the e-mail address used and the FEMS number concerned, we will create the link and other users can then use the Online Monitoring of an installation.
9.1.2. Access for the installer
The installer account can be created as described in the section Configuration via commissioning wizard on the FENECON homepage. Access is required for successful commissioning.
10. Capacity expansion of the system
The capacity can also be extended at a later date, there is no time limit.
The maximum capacity is not reached with additional new battery modules, as new modules are equal to the old modules.
10.1. Capacity expansion of the battery tower
by one or more battery modules
The battery tower can be expanded to up to 14 battery modules in one battery tower.
If the electrical energy storage system is expanded with additional battery modules after commissioning, proceed as follows:
After a capacity expansion, the commissioning protocol must be carried out again. |
![]() |
|
![]() |
|
![]() |
|
![]() |
|
![]() |
|
![]() |
|
The capacity can also be extended at a later date; there is no time limit here. You will not reach the full capacity with the new battery module, as the new module adapts to the old modules.
If the battery tower is extended by additional battery modules after several weeks or months, the following procedure must be followed:
29-30 % SoC |
|
![]() |
|
![]() |
|
![]() |
|
![]() |
|
![]() |
|
|
11. Capacity expansion of the system
by one or more battery towers
The capacity of the system can be subsequently expanded by one or more battery towers with the same capacity. There is no time limit here.
The maximum expansion of the FENECON Home 6, 10 & 15 system comprises up to 4 battery towers, each with 3 to 14 battery modules and a maximum of 156.8 kWh.
The full capacity is not achieved with new battery modules, as the new modules become similar to the old modules.
Proceed as follows before the extension:
![]() |
|
![]() |
|
![]() |
|
![]() |
|
|
12. FEMS extensions
For the following FEMS extensions, the integrated relays can be used directly on the (first) battery tower.
Various pins on the Harting plugs are provided for this purpose.
-
Harting plug 10-pin: 3 x free relay channels (max.: 230 V; 10 A)
-
Harting plug 16-pin: 2 x control contacts (max.: 24 V; 1 A)
-
3 x Digitaler Eingang für Rundsteuerempfänger
-
1 x Digitaler Eingang für § 14a
-
1 x analog output (0-10 V)
-
It may not be possible to connect and operate all apps at the same time.
For more information on the following apps, please visit our homepage.
If the integrated relays are not sufficient, an external 8-channel relay board can be connected via Ethernet. |
![]() |
The pin assignment of the Harting plug (10-pin) is shown in detail below. |
Item | Description |
---|---|
1 |
230 V supply for internal components |
2 |
Relay 1 (230 V; 10 A) |
3 |
Relay 2 (230 V; 10 A) |
4 |
Relay 3 (230 V; 10 A) |
5 |
Neutral conductor connection (required for integrated meter) |
6 |
PE connection |
![]() |
The pin assignment of the Harting plug (16-pin) is shown in detail below. |
Pos. | Beschreibung |
---|---|
1 |
RS485 Anschluss — Wechselrichter |
2 |
RS485 Anschluss — Externe Geräte |
3 |
Analoger Ausgang (0 bis 10 V) |
4 |
12 V DC (12 V; GND) |
5 |
3 x digitale Eingänge |
6 |
Digitaler Eingang für § 14a |
7 |
Relais 5 (24 V; 1 A) |
8 |
Relais 6 (24 V; 1 A) |
9 |
PE-Anschluss |
12.1. Connection of a heat pump via "SG-Ready"
The integration of an "SG-Ready" (smart grid-ready) heat pump is an advanced form of sector coupling of electricity and heat - often also referred to as a "power-to-heat" application. The control system ensures that the heat pump slightly overheats the thermal energy storage at times when cheap (solar) electricity is available in order to save electrical energy at times when there is no cheap surplus electricity.
![]() |
|
Once the components have been installed, the app still needs to be installed. |
12.2. Connection of a heating element with a maximum of 6 kW
The integration of an electric heating element is the simplest and cheapest form of sector coupling of electricity and heat — often also called a "power-to-heat" application.
If the capacity of the electrical energy storage is exhausted, self-generated energy must be fed into the public grid with low remuneration. In these cases, it often makes sense to use the surplus electricity for water heating (e. g. for hot water buffer tanks, pool heating, etc.). In this way, other energy sources (e. g. wood or oil) can be saved.
![]() |
|
Care must be taken to ensure that three different phases are used. If only one phase is used, damage may occur. |
Once the components have been installed, the app still needs to be installed. |
Manual mode is only suitable for temporary operation. For permanent operation, the external relay control must be used. |
12.3. Control of a heating element greater than 6 kW
(control via external relay)
The integration of an electric heating element is the simplest and cheapest form of sector coupling of electricity and heat — often also called a "power-to-heat" application.
If the capacity of the electrical energy storage is exhausted, self-generated energy must be fed into the public grid with low remuneration. In these cases, it often makes sense to use the surplus electricity for water heating (e. g. for hot water buffer tanks, pool heating, etc.). In this way, other energy sources (e. g. wood or oil) can be saved. The externally installed relays must be designed according to the installed power of the installed heating element.
![]() |
|
![]() |
|
![]() |
|
Once the components have been installed, the app still needs to be installed. |
12.4. Control of a CHP unit
The integration of a Combined Heat and Power unit (CHP) into electrical energy management is an advanced form of sector coupling of electricity and heat.
This allows to utilize the property of the CHP unit as an electrical generator that is independent of the time of day and weather conditions. When the state of charge of the electrical energy storage system is low, the CHP is given a signal to switch on to produce electricity. This is useful, for example, if the battery capacity is not sufficient to cover electricity consumption at night. This avoids the need to purchase expensive electricity from the grid.
When the battery is charging, this signal is stopped again to prevent the CHP electricity from being fed into the grid unnecessarily.
![]() |
|
Once the components have been installed, the app still needs to be installed. |
12.5. Additional AC meter
-
If additional meters have been installed for monitoring other consumer loads or generators, these must be integrated into the circuit in accordance with the manufacturer’s instructions.
-
The communicative integration is shown below using a 3-phase sensor without a current transformer as an example.
-
Only meters approved by FENECON can be integrated.
-
The first generation meter is always integrated with Modbus ID 6. All others in ascending order. The baud rate is 9600.
![]() |
|
![]() |
For example SOCOMEC E24
|
![]() |
Example: KDK 4PU
|
Wenn mehrere Zähler verbaut werden sollen, dann können diese kommunikativ in Reihe geschaltet werden. Hierfür kann vom ersten Zähler auf den Zweiten usw. weitergebrückt werden. Die Modbus-Adresse muss aufsteigend eingestellt werden. |
Once the components have been installed, the app still needs to be installed.
|
12.6. Activation of the app in the FEMS App Center
After installing the hardware FEMS extension, it still needs to be activated in the App Center. To do this, proceed as follows:
![]() |
|
![]() |
|
![]() |
|
![]() |
|
![]() |
|
![]() |
|
![]() |
|
|
|
|
12.7. Installation of further FEMS apps
When you ordered the FEMS app, you received a 16-digit license key. You can use this license key to redeem the app independently in the FEMS App Center.
![]() |
|
![]() |
|
![]() |
|
![]() |
|
![]() |
|
![]() |
|
![]() |
|
![]() |
|
![]() |
|
![]() |
|
13. External control of the inverter
There are various ways to override the inverter from external devices.
13.1. Ripple control receiver
The inverter can be controlled directly via a ripple control receiver. The following plugs supplied with the inverter are required for this.
![]() |
|
![]() |
|
The active power of the inverter can be controlled directly by the grid operator via a ripple control receiver.
The behavior of the inverter in the various control stages is described as follows:
-
100 % → Standard signal, inverter works without restrictions.
-
60 % → Inverter output power is reduced to 60 %.
-
30 % → Inverter output power is reduced to 30 %.
-
0 % → Inverter output power is reduced to 0 %.
If other inverters are used, these must also be connected separately to the RCR; how exactly depends on the grid operator and the RCR used.
In the event of a curtailment to 0 %, the grid feed-in of the inverter is stopped completely, i.e. the consumer loads are supplied completely from the grid. |
![]() |
|
![]() |
|
![]() |
|
![]() |
Variant A
|
![]() |
Variant B
|
![]() |
Variante A
|
![]() |
Variant B
|
![]() |
|
13.2. Remote shutdown
The inverter can be disconnected from the grid when remote disconnection is activated, e. g. via a central grid and plant protection. One of the following plugs supplied with the inverter is required for this.
![]() |
Variant A
|
![]() |
Variant B
|
![]() |
|
The emergency power output is still active (if activated) and supplies the emergency power to the consumer loads. |
![]() |
|
![]() |
Variant A
|
![]() |
Variant B
|
![]() |
Variant A
|
![]() |
Variant B
|
![]() |
|
This method can also be used to connect P,ave monitoring. |
13.3. § 14a of the Energy Industry Act (EnWG)
The Inverter can be limited to a maximum reference power of 4.2 kW. The digital input of the EMS must be assigned for this.
![]() |
|
14. Troubleshooting
14.1. Errors in Online Monitoring
The system status can be checked after logging in at the top right using the color of the symbol. A green tick indicates that everything is OK, an orange exclamation mark indicates a warning (Warning) and a red exclamation mark indicates an error (Fault).
14.1.2. Troubleshooting
![]() |
You can get a detailed overview of an existing warning or error by clicking on the exclamation mark in the top right-hand corner. |
![]() |
The scroll bar can be used to examine the origin of the warning or error in more detail. |
![]() |
Clicking on the icon (down arrow) displays a more detailed error description depending on the error. |
In the example above, an incorrect reference for the network counter was intentionally entered for test purposes, which is why the controller fails to run.
![]() |
Under certain circumstances it can happen that the FEMS is not accessible and the adjacent error message appears. |
If the FEMS is offline, follow the steps displayed below the message.
14.2. FENECON Home 6, 10 & 15 inverter
14.2.1. Fault display
Faults are indicated by a red LED next to "SYSTEM".
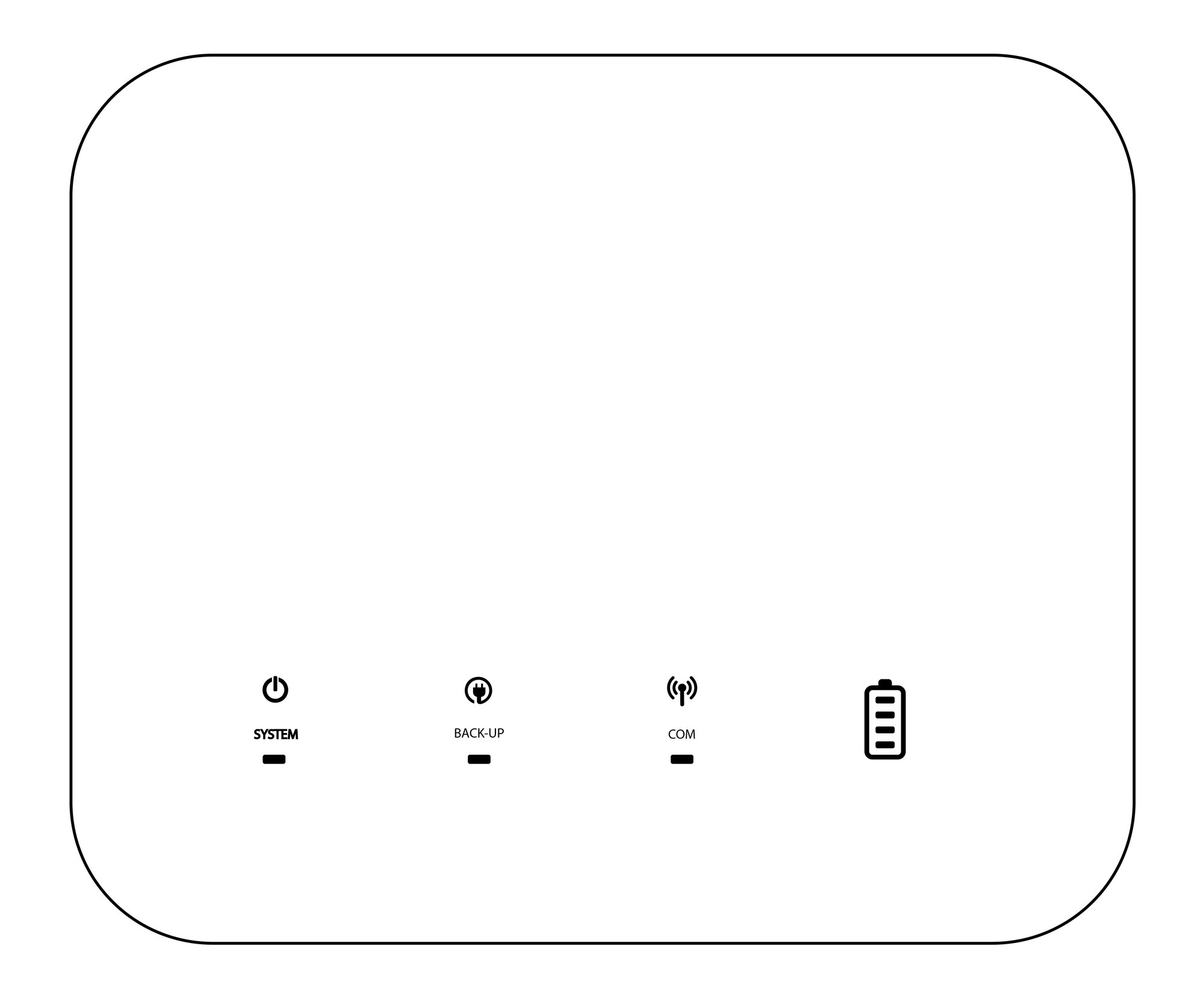
Rotary field of the grid connection
-
Check whether a clockwise rotating field is present at the grid connection.
-
Otherwise, contact the FENECON Service. The contact details can be found in the Service section. The LEDs display further information on the status of the inverter.
Display | Status | Description |
---|---|---|
The inverter is switched on and in standby mode. |
||
The inverter is starting and is in self-test mode. |
||
The inverter is running normally in grid-parallel or stand-alone mode. |
||
Overloading of the RESERVE output. |
||
An error has occurred. |
||
The inverter is switched off. |
||
The grid is abnormal and the inverter is in stand-alone mode. |
||
The grid is normal and the inverter is in parallel mains operation. |
||
RESERVE is switched off. |
||
The inverter is not connected to the internet. Communication takes place via the EMS box. Therefore, there is no LED indication here. |
14.3. Battery tower
14.3.1. Fault display
Errors are displayed on the FENECON Home 10 BMS box via a red LED.
The various errors are indicated by LED codes.
System status | System info | LEDs | |||||
---|---|---|---|---|---|---|---|
blue/red |
1 |
2 |
3 |
4 |
|||
Boot loader |
|||||||
Start |
Master/Slave |
||||||
Parallel box |
|||||||
Extension Box |
|||||||
Test mode |
Single or parallel connection |
||||||
SoC display |
|||||||
Charge |
0 % to 25.0 % SoC |
||||||
25.1 % to 50.0 % SoC |
|||||||
50.1 % to 75.0 % SoC |
|||||||
75.1 % bis 99.9 % SoC |
|||||||
100 % SoC |
|||||||
Discharging and standby |
100 % to 75.1% |
||||||
75.0% to 50.1% |
|||||||
50.0% to 25.1% |
|||||||
25.0% to 0 % |
|||||||
Error |
Overvoltage |
||||||
Undervoltage |
|||||||
Overtemperature |
|||||||
Undertemperature |
|||||||
Overcurrent |
|||||||
SoH too low |
|||||||
Int. communication |
|||||||
Ext. communication |
|||||||
Address error Parallel |
|||||||
Address error Modules |
|||||||
BMS box fuse |
|||||||
Module fuse |
|||||||
Contact error |
|||||||
Insulation error |
|||||||
BMS error |
Blue, permanently on |
|
Blue, blinking |
|
Blue, flashing quickly |
|
Red, permanently on |
14.3.2. Troubleshooting
If faults cannot be rectified or in the event of faults that are not included in the fault list, the FENECON Service must be contacted. See section Service.
14.4. Fault list
Component | Disturbance | Measure |
---|---|---|
Battery module |
The battery module has become wet |
Do not touch |
Battery module |
The battery module is damaged |
A damaged battery module is dangerous and must be handled with the utmost care. |
14.5. Service
The FENECON service must be contacted in the event of system faults:
Phone: +49 (0) 9903 6280-0
E-mail: service@fenecon.de
Our service hours:
Mon. to Thurs. 08:00 to 12:00 h | 13:00 to 17:00 h
Fri. 08:00 to 12:00 h | 13:00 to 15:00 h
15. Technical maintenance
15.1. Tests and inspections
When carrying out inspection work, ensure that the product is in a safe condition. Improperly performed inspections can have serious consequences for people, the environment and the product itself. |
Inspection work must only be carried out by trained and qualified specialists. |
The maintenance instructions of the component manufacturer must be observed for all individual components. |
The Guarantee holder is the end customer who has not purchased the system for the purpose of resale, but for his own use. Dealers, regardless of type and trading level, cannot derive any claims from this Guarantee.
15.2. Cleaning
Cleaning agents: The use of cleaning agents can damage the electrical energy storage unit and its parts.
It is recommended that the electrical energy storage unit and all its parts are only cleaned with a cloth moistened with clean water.
The entire product must be cleaned regularly. Only suitable cleaning agents may be used for this purpose. |
15.3. Maintenance work
No regular maintenance work needs to be carried out on the system, but check the status of your electrical energy storage system regularly.
The capacity guarantee applies if the capacity of a battery module falls below 70 % of the amount of energy shown as usable capacity before reaching 6,000 full cycles on the battery output side (DC) if a 2.2 kWh battery module has a capacity of less than 1.54 kWh. For the FENECON Home 6, 10 & 15 and FENECON Home 20 & 30 models, the amount of energy falls below 70 % of the usable capacity if a 2.8 kWh battery module has a capacity of less than 1.96 kWh. |
16. Information for fire departments when handling FENECON Home and Commercial battery energy storage systems
The FENECON Home and Commercial systems operate in the low-voltage range, which means that they are operated with voltages of less than 1,500 volts direct current (DC) and less than 1,000 volts alternating current (AC).
It may be useful to install an additional switch that disconnects the building from the emergency power supply. This makes it easier for the fire department to act safely and quickly in an emergency.
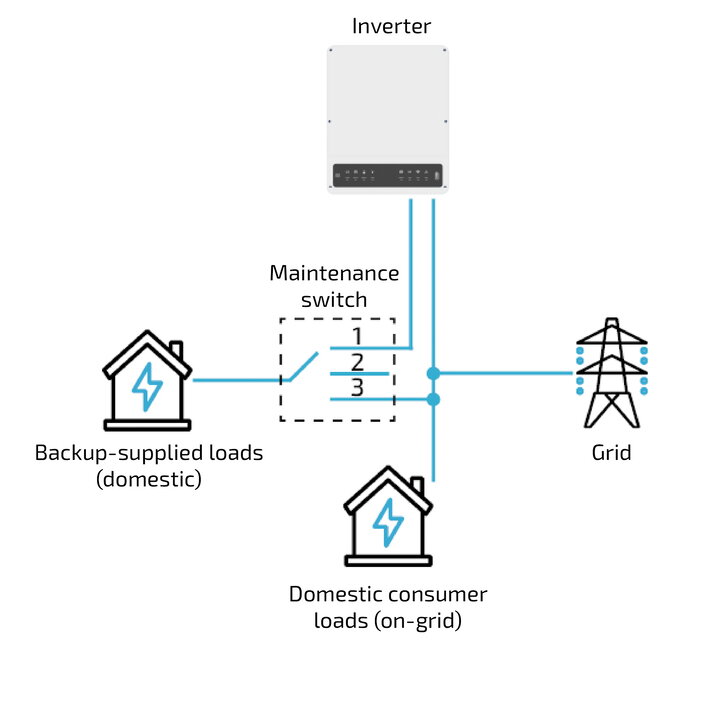
For a precise procedure for emergency services, it is recommended to ask the relevant fire department schools and request the corresponding information sheets and pocket cards for battery storage systems.
18. Transportation
This section contains information on external and internal transportation of the product.
Transportation is the movement of the product by manual or technical means.
-
Only use suitable and tested lifting gear and hoists for transportation!
Risk due to lifted Loads! |
Check that the parts and outer packaging are in perfect condition. |
See for yourself that
|
Notes:
|
Legal regulations |
19. Dismantling and disposal
19.1. Prerequisites
-
The power supply to the Battery energy storage unit is interrupted and secured against being switched on again.
Sharp and pointed edges
|
19.2. Dismantling
-
The electrical Energy storage system must only be dismantled by authorized electricians.
-
Dismantling work may only be carried out when the system has been taken out of operation.
-
Before starting disassembly, all components to be removed must be secured against falling, tipping over or moving.
-
Dismantling work may only be carried out when the system is shut down and only by service personnel.
-
The dismantling instructions of the component manufacturers (see appendix, Other applicable documents) must be observed.
-
The current laws, regulations and standards must be observed when transporting the battery modules (e.g. Dangerous Goods Transportation Act - GGBefG).
19.3. Waste disposal
-
The FENECON system must not be disposed of with normal household waste.
-
The FENECON Home 20 & 30 is RoHS- and REACH-compliant.
-
Disposal of the product must comply with local regulations for disposal.
-
Avoid exposing the battery modules to high temperatures or direct sunlight.
-
Avoid exposing the battery modules to high humidity or corrosive atmospheres.
-
Dispose of the electrical energy storage system and the batteries it contains in an environmentally friendly manner.
-
Contact FENECON GmbH to dispose of the used batteries.
|